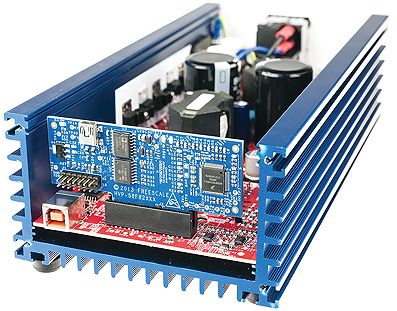
The 3-phase motor has become more and more popular and has started to push out the old-fashioned 1-phase AC or DC drives. These 3-phase drives are targeted at refrigerators, washers, dishwashers, industrial drives, and almost all the moving things around us. However, the hardware in these electronic devices gets complicated and the software offers endless possibilities of functionality. Development of these devices consumes more time and requires ever more effort from the engineers. To speed up the development time and decrease the costs, Freescale has designed a cost effective high-voltage motor control development platform supporting the new ARM®-based motor control and digital power conversion Kinetis®-V family and also the Digital Signal Controller – 56F8000EX family.
Authors:
Ivan Lovas and Pavel Sustek, System Application Engineers, Freescale Semiconductor
Dobrucky Branislav and Peter Cubon, University consultants, University of Zilina
Acknowledgement:
I would like to offer my special thanks to Centre of Excellence of Power Electronic Systems and Materials for their Components II, No. ITMS 26220120046.
Design concept
Freescale’s high-voltage motor control platform is a new 1000 W, 3-phase power stage that will operate off DC input voltages from 110-390V, and with AC line voltages from 90-240V. In combination with one of the controller cards, it provides a software-development platform that allows algorithms to be written and tested without the designing and building of their own hardware. It supports a variety of sensorless and sensored algorithms for AC induction, PMSM and brushless DC (BLDC) motors, which can be found on the Freescale web pages freescale.com/motorcontrol.
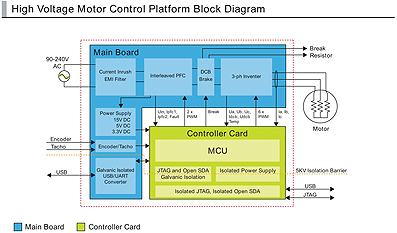
The power stage consists of the main board and interchangeable controller cards accommodating the target microcontroller.
Main board specifications:
The main board contains an input filter, input rectifier, brake switch, IPM with IGBT-gate-drive circuits, analog-signal conditioning, low-voltage power supplies and many features for easy debugging. In addition, the HV AC power stage includes an active interleaved (CCM or CRM) power factor correction (PFC) circuit that facilitates development of PFC algorithms. The main board also contains hardware over-current and overvoltage protection, temperature monitoring and galvanic isolation.
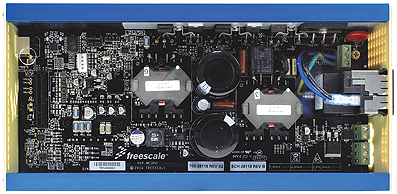
Key Features:
• Input voltage AC: 90-240V / DC: 110-390VDC
• Output power up to 1kW
• On-board Interleaved Power Factor Correction supporting DCM, CCM, CRM
• Inrush limitation using an NTC resistor + Relay
• Optical isolation 5KV for communication and debugging
• Support communication with external devices ( for example, a Bluetooth wireless module)
• Hardware over-current, overvoltage faults
• Motor speed/position sensors interface (Encoder, Hall, Tacho generator)
• Analog sensing (input voltage, DCB voltage, DCB current, phase currents, back-EMF voltage, PFC currents, IGBT module temperature monitoring)
• Supports multiple MCU cards using the PCI Express 64
• EMI filter
Controller cards specifications
Controller cards are an integral part of a high-voltage development platform. A wide portfolio of supported controllers helps ensures that the specific requirements for each application are met. Various controllers are supported, starting with ARM Cortex-M0+ cores, the DSCs, and up to ARM Cortex-M4 cores, with wide connectivity possibilities. Controller cards are connected via the 64-pin PCI Express connector and they are divided into two families, Cortex-based and DSC-based.
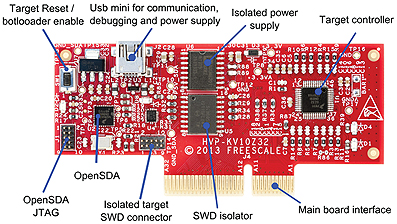
Key features:
• Accommodates a Target Freescale MCU(KV10, KV3x, KV4x, 56F827xx, 56F84xxx)
• SWD/JTAG isolation up to 5kV
• Cortex-based versions accommodate the integrated Open SDA, supporting
– Mass storage boot loader
– Debugger
– Virtual serial link
• Compatible with CW 10.x, IAR, Keil, KDS
• Design optimized for low noise
• On board isolated power supply, allowing safe debugging
• Daughter card allowing a stand-alone operation
• Test points

Fast prototyping and fast development are essential requirements for success.
Developing and debugging a high-voltage application with this tool becomes really fast, easy and safe. Moreover, easy porting from one controller to another, with motor control library support, the FreeMASTER and MCAT development tools, significantly contributes towards finalization of the development far earlier than ever before.
This motor control kit is also suitable for those who want to easily learn and develop their motor control application soon, verify existing motor control techniques, or to implement a new one.
The development platform is planned for availability in Q4 2014. More information can be found at www.freescale.com