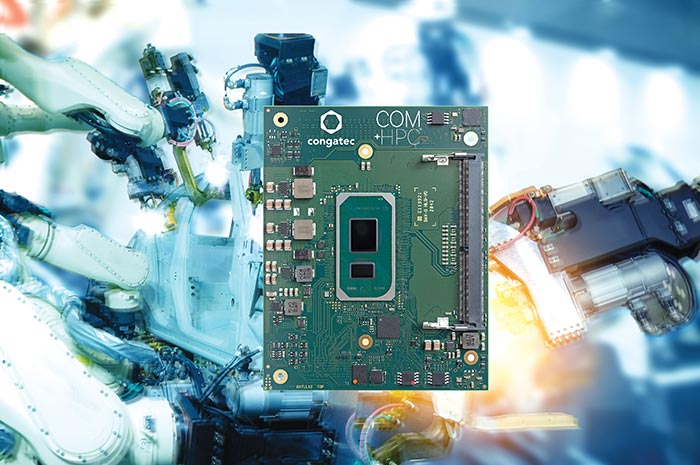
Three-dimensional awareness has extremely high computing demands. The 12th generation Intel Core processing technology in COM-HPC modules from congatec transfers twice as much data due to PCIe Gen5. (© Ekkasit919/dreamstime/congatec)
Machine vision in three dimensions can’t compare to the performance of human eyes, but it comes the closest from technology that’s currently available. As a result, it’s used for many types of tasks and is paired with machine learning more and more often. The manufacturing industry directly benefits from this advance, with Vision Guided Robotics (VGR) and Automated Guided Vehicles (AGV) utilizing improved three-dimensional awareness for increasing the performance of Industry 4.0 applications. Helping with the migration of this technology to hardware by significantly amplifying its processing power is the latest batch of COM-HPC modules from manufacturers like congatec.
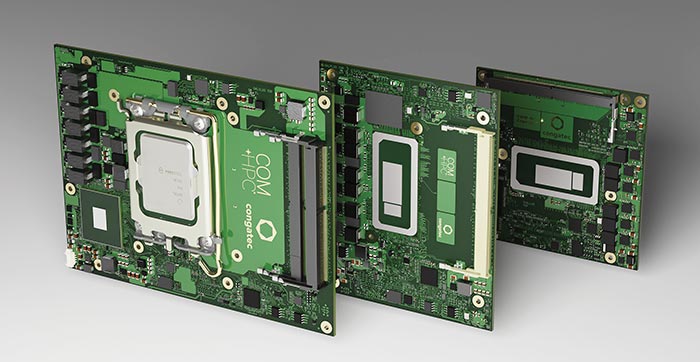
Computer-on-Modules that adhere to the new PICMG COM-HPC Client specification are available from congatec with 12 Gen Intel Core processors (Alder Lake). Increased availability and equalized performance of durable modular edge servers in vision guided robotics systems and mobile logistics vehicles are guaranteed by their standardized footprint. (© congatec)
The use of 3D vision is on the rise, with an increase of close to 15% year-on-year. Two factors at play are a decrease in citizens actively working and an increase in citizens requiring health care. Additional robots are therefore required, due to a reduction in the workforce. Robots achieve much higher production efficiency than humans in the manufacturing industry, while robots provide care and promote autonomy/mobility in healthcare.
Bringing the future into focus
However, there is still a lot of development work to be done before robots can perform any heavy work. For example, inspection systems are stationary and immovable. While Vision Guided Robotics (VGR) does offer more mobility, and is experiencing dynamic development, its movement is still rather limited. The main function of immobile robots is to watch things closely. The use of 3D cameras allows them to perform this task more efficiently by identifying objects from three axis and measuring lengths. A thirst for increased flexibility in discrete manufacturing is driving industry growth in this area, which mainly comes from the importance it has gained as a result of the Industry 4.0 trend of moving closer to batch size 1.
Feeding and output systems in discrete manufacturing are mainly VGR and automated guided vehicles (AGV), with a projected growth rate of 14.1% per year until 2027. Permanently installed conveyor systems will be minimized, or eliminated, due to the implementation of AGVs for moving and transporting products. Due to their mobility, they do no block areas like conveyor systems. They move along pre-programmed routes that optimize warehousing, transport, and other tasks. When used with mobile pick & place robots, integration with VGR systems is the result.
Modularity plays a crucial role
Advanced mobile robotic systems may require additional subsystems. A good case to highlight is a robot that was constructed with four legs and featured a total of three Computer-on-Modules. Each module performed a specific task – locational awareness, motion control and task fulfilment. This example demonstrates the advantageous use of Computer-on-Modules, which can be easily scaled for each specific task. Controls could also be combined within a single system for communication with the drives’ actuators/frequency inverters in real-time using a two-wire Ethernet, although modules with significantly more power on a time-proven platform strategy would be required. It should be noted that all in all 10 processor cores on 3 modules, which have not been introduced on the market for ultra low-power mobile embedded systems, were used in this example to deliver the required computing power and ensure real time operation.
Supercharging multi-purpose with higher core counts
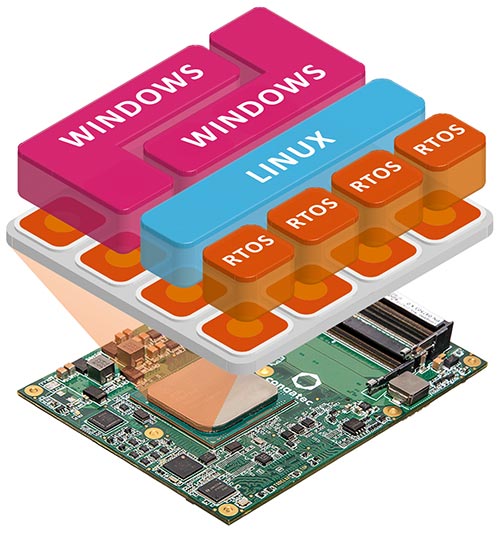
Computer-on-Modules from congatec are compatible with Real-Time Systems’ real-time hypervisor technology for combining multiple edge applications in a single system. (© congatec)
COM-HPC modules that eclipse current COM Express module performance with substantially more interfaces, bandwidth, memory and cores are starting to become available after the PICMG standardization committee ratified the COM-HPC Computer-on-Module specification.
This is true for COM-HPC client modules, but affects the server category even more, as future solderable entry class COM-HPC server modules will be more durable and scalable, allowing for consolidation of decentralized real-time control systems in multi-purpose embedded edge computer solutions. Hypervisors from manufacturers like Real-Time Systems would be required for virtual machines capable of real-time operation. Real-time hypervisor solutions are required for uninterrupted, deterministic real-time control, regardless of rebooting on the same HMI processor of the production cell or the evaluation and conversion or data or processing of tasks in parallel by the integrated loT gateway.
A growing hunger for higher performance
Processor hungry 3D imaging needs the power of COM-HPC. Just consider the creation of point clouds acquired by time-of-flight (ToF) technology, which outputs 32 bits of spatial coordinates for each pixel. A resolution of 640 x 480 pixels at 30 frames per second (fps) therefore produces 35 MB of 3D data per second. On top of this the color information of a classic 2D camera, with generally 4 times higher resolutions has to be processed as well. At 1.2 mega pixels (1280 x 1024 pixels) and 8-bit color depth per channel, we are talking about an additional 112.5 MByte per second. These result in up to around 150 megabytes of data that is to be processed per second, not to mention the excessive processing power required for two cameras operating in stereo. Since the amount of data and CPU / GPGPU computing power are extremely demanding, the brand new generation of COM-HPC modules utilizing 12th generation Intel Core processor technology (Alder Lake) are preferred. Their standout attributes include providing PCIe Gen 5 with four times as much bandwidth between processors and cameras, as well as discrete GPUs, compared to PCIe Gen3. Native support of MIPI-CSI cameras also provides two main benefits – reduction of processing requirements and the need for investments in camera technology. Customizable connections of 1GbE and 2x 2.5GbE (with TSN) Ethernet options to dual 10GbE, which are coming from congatec’s COM-HPC starter set, are compatible with the modules. Interfacing with smaller devices, such as actuators and sensors, is therefore possible if two-wire Ethernet is used.
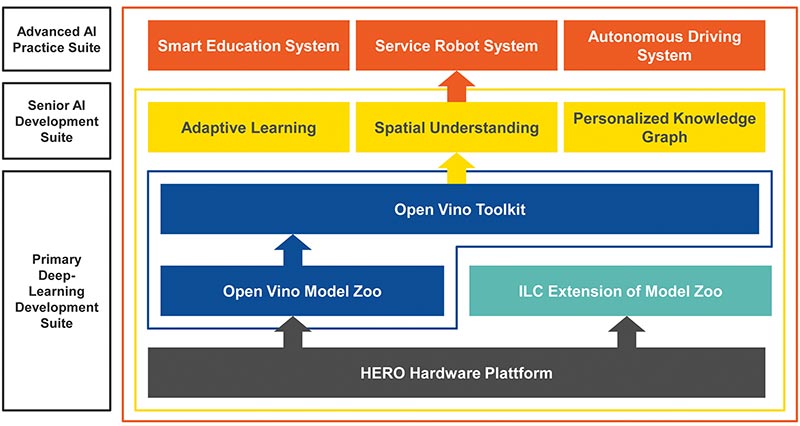
A three level training kit, based on congatec Computer-on-Modules, was created by the Autonomous System Lab at Intel Labs China. (© congatec)
Keeping AI firmly in the mix
congatec has ensured additional plug-and-play friendliness with IIoT and Industry 4.0 networked embedded systems by providing extensive AI compatibility with cameras connected by MIPI-CSI. Intel DL Boost based vector neural network instructions (VNNI) and 8-bit integer instructions (Int8) can be implemented on the GPU for AI and inference acceleration. Compatibility with the Intel Open Vino ecosystem for AI should also be mentioned. A COM Express based platform for training purposes, together with a “Ready for Production” kit certified by Intel for workload consolidation, have already been introduced by the Autonomous System Lab of Intel Labs China. With this HERO platform, engineers can now evaluate this OpenVINO ecosystem from the software libraries to Adaptive Human-Robot Interaction (AHRI) or Simultaneous Localization & Navigation (SLAM).
Evaluation by the ATX carrier board conga-HPC/EVAL-Client
Smart vision robotics and autonomous logistics vehicles can be also evaluated by the ATX carrier board conga-HPC/EVAL-Client. It comes with two massively performant PCIe Gen4 x16 interfaces and many LAN options for data bandwidth, transmission, and connectors. Mezzanine cards allow the carrier to run up to two 25GbE interfaces. The conga-HPC/cTLU Computer-on-Module is the main component of the starter kit presented for COM-HPC Client designs. Three processor configurations are available, with three cooling solutions to go with the configurable 12 to 28 W TPD range of the 11th generation Intel® Core™ processors.
Three-dimensional applications from Basler – congatec’s embedded vision partner
A Deep Learning-based vision system with a Basler blaze time-of-flight (ToF) camera that can be effortlessly combined with congatec’s embedded systems. High-resolution, three-dimensional images are acquired by the Basler blaze camera with close to millimeter accuracy. In addition to the output of a greyscale intensity image, ToF technology analyzes pulses of light in the near infrared spectrum for calculating the distance to each pixel. Unlike 2D RGB images, shape data takes the place of color information, so both red and green apples are detected at the same time. Further applications are also utilized, such as the dimensions and precise location of objects. The Basler blaze camera features an easy to use interface that runs on all operating systems for trouble-free integration of Data Spree’s Deep Learning DS software. This software solution, which is based on deep neural networks, requires zero knowledge for the development of Deep Learning models. The various development stages of the system – acquiring data, annotating, training, and deployment to application of the trained network on the target hardware – are noticeably simplified.
BCON for MIPI allows for trouble-free connection of cameras
Models from Basler’s Dart series are an advantageous first step when adding the processing of images to standard processors. There use is not dependent on how the COM is constructed or the design of the carrier-based embedded system. The custom BCON for MIPI interface from Basler, which is based on the MIPI CSI-2 interface standard, allows for trouble-free integration. BCON for MIPI models are as easy and convenient to deploy as a plug-and-play camera interface, such as USB 3.0 BCON (Basler Connectivity), thereby adding the powerful and well-proven machine vision features from the embedded industry’s established data transmission standards (i.e., LVDS or MIPI CSI-2). Due to integration with machine vision standards (GeniCam), and the pylon SDK, you are provided with easy and convenient access to standard technologies. Extremely secure data throughput with elevated bandwidth is the final result.
Author
Zeljko Loncaric
Marketing Engineer at congatec.