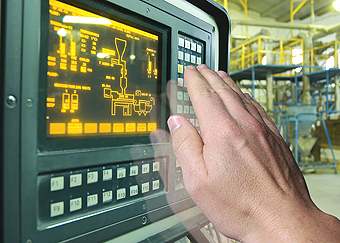
Often industrial machinery needs to be operated in tough environments where either potentially harmful substances to the machine are present or where the operator has to constantly monitor a process finding it hard to look at a screen. A new solution from Microchip based on the GestIC® chip (MGC3130) and the Colibri software suite has the potential to significantly change the HMI (human machine interface) concepts in industrial environments by using gestures instead of touch operations in order to control and operate machinery and equipment.
The MGC3130 is the world’s first 3D gesture controller to utilize electric fields (E-fields) for hand position tracking with free-space gesture recognition, which offers several advantages – particularly for the industrial environment. Because the MGC3130 only detects changes in nearby E-fields caused by conductive objects, such as the human body, it is resistant to environmental influences, such as light and sound. Additionally, because its range is 15cm, the MGC3130 can ensure that only gestures from the intended user are detected, such as preventing false detects for operator functions from others in the vicinity. Conversely, there are no blind spots within that 15cm, unlike other gesture technologies. Another big advantage of GestIC technology is that it uses electrodes for sensing, as they can remain invisible by using a display’s existing Indium Tin Oxide (ITO) coating or by being integrated behind the device’s housing. This is great for industrial applications where the control unit for machinery could be contained within a sealed unit.
Compared to other 3D gesture technologies, such as infrared, ultrasound or camera-based solutions, GestIC technology provides several additional advantages for industrial applications. For example, camera-based solutions need a certain amount of light in order to operate properly while simultaneously requiring dynamic light compensation. Furthermore, a camera has a fixed angle of view, which creates blind spots, particularly in industrial environments where the users are very close to the camera. Conversely, it is difficult for camera solutions to eliminate false detects from other activity going on behind the operator. GestIC® technology also provides output data with a high refresh rate of 200Hz, while consuming up to 90% less power than camera-based solutions.
The Physics behind it
The basic sensor setup is described in figure 1: An isolation layer separates a single full-plane transmitter electrode located over a ground layer from the receiver electrodes
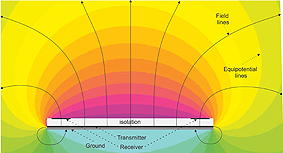
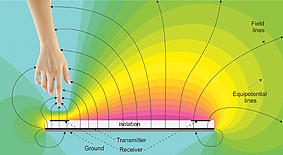
located on the top layer. Controlled by the MGC3130, the transmitter electrode generates an electrical field with a frequency of 100kHz. Without any external disturbances, this electrical field looks like the evenly distributed field in figure 1. Whenever an object enters this electrical field, it disturbs the field lines. A typical example of such a disturbance is shown in figure 2.
Due to the disturbance, the formerly even distribution of the equipotential lines as well as the field lines has significantly changed. By entering the electrical field, the conductive object (in the applicable cases: a hand) absorbs the electrical field as it conducts electrical charges to ground, resulting in a change of both the electrical field and the equipotential lines. The MGC3130, measures the minuscule signal deviations at the receiver electrodes generated by the hand and processes the results. The closer the hand gets to the receive electrode, the higher the local influence of the hand.
Utilising four receiver electrodes (north, south, east and west) the MGC3130 allows tracking of the hand’s position in X, Y and Z direction within the sensing area. In a further computing step, the MGC3130 identifies gestures by applying a Hidden Markov Model (HMM) based gesture recognition engine which allows an exceptionally high, user independent gesture recognition. When, for example, the hand flicks from the right to the left, there is a high signal deviation on the right side at the beginning.
This signal deviation on the right electrode decreases during the movement, while the signal deviation on the left electrode simultaneously increases. Movement patterns like this are recognized and calculated on-chip, and provided in a predetermined manner at the outputs.
The X/Y/Z tracking resolution is up to 150 dpi, depending on the electrodes’ design and the hand’s position. The closer the hands position relative to the sensing area, the higher the signal to noise ratio and the higher the resolution.
GestIC technology enables this mouse-like accuracy without almost any jitter. For demonstration purposes, the design team controlled a notebook PC’s cursor jitter-free, just by moving the hand and without the use of a mouse.
The Electrodes
The receive electrodes are always located above the transmitter electrode (figure 3). For example, in the demonstration setup that Microchip showed at the Electronica trade show, the receive electrodes consisted of copper layers on the upper side of a PCB. Electrodes can be realized by using any type of solid conductive material such as solid PCBs, flexible printed circuit boards (FPCs), LDS electrodes (laser direct structured), conductive foils, and the aforementioned ITO layer already found in displays.
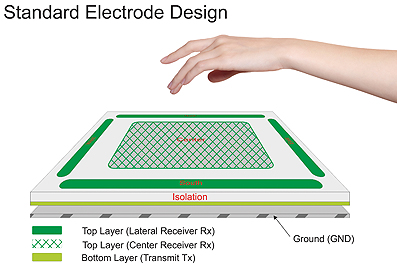
Microchip’s GestIC technology is able to work with thin sensing which allows for an invisible integration behind the target device’s housing, without increasing the overall thickness of the product’s design. Therefore, the electrodes are not only low-cost but also low-impact in terms of the overall design. This is of high importance in industrial electronics, where these electrodes can be hidden behind areas such as the control panel.
As mentioned earlier, the reuse of existing conductive structures, such as the ITO coating of a displays touch panel, makes GestIC technology a very cost-effective system solution. Currently, Microchip is working with major display manufacturers, on the pre-integration of GestIC technology into a complete display module.
By connecting the MGC3130 to the ITO coating, the touch area of the display is transformed into an electrical-field electrode sensor field without disturbing the multi-touch functionalities of the underlying touch display. Due to its seamless integration, GestIC technology initiates the third dimension of sensing as soon as the fingers are removed from the display surface.
In industrial applications, this can enable the system to display different items based on the direction from which the hand approaches. While a vertical approach might enable the control menu, an approach from the lower left side could enable the system’s setup menu. Another possibility is switching between basic menus by using flicking gestures in the air.
GestIC technology is very flexible, as it not only recognizes linear gestures but also symbol gestures, circular gestures and others. In the industrial environment this capability may be used in order to increase/decrease the output quantities of a dispensing system or a valve, for example, by simply drawing a virtual knob in the air. Basically, it enables the operator to keep the eyes on the process while simultaneously giving commands to the system by making the relevant gestures.
The MGC3130 Chip
The MGC3130 is a configurable mixed-signal controller consisting of an analog front end with one transmit and five-receive channels and a digital Signal Processing Unit (SPU). Four of these five channels are used for recognizing gestures or the hand’s position, while the fifth channel enables touch detection and improves low distance accuracy. Each channel undergoes signal conditioning. The pre-conditioned analog signals are then digitized and processed by the integrated SPU.
At the output, the SPU provides the calculated results via I2Ctm or SPI interfaces. Microchip provides an API (application programming interface) running on the application or host controller. This API allows the design engineer to easily map the relevant signals to the target destination. This means that designers do not have to concern themselves with the signal conditioning, as Microchip pre-processes the X/Y/Z hand position data as well as comprehensive gesture-recognition software on chip, known as the Colibri suite. In order to enable designers to create highly individual special features through application-specific post processing, Microchip also passes through the filtered electrode signals to the outputs.
The Colibri Suite Software
The Colibri suite uses a Hidden Markov model (HMM) based gesture recognition engine, in conjunction with X/Y/Z hand-position vectors. HMM provides the highest user-independent recognition rates for 3D hand and finger gestures. This means that GestIC technology consistently provides exceptionally high gesture-recognition rates, regardless of who is using the machinery.
At the MCG3130’s digital output, the Colibri suite delivers high-resolution X/Y/Z hand position tracking data as well as flick, circle and symbol gesture words. For flick gestures, the Colibri suite not only detects basic movements, such as left, right, up and down, but also more sophisticated flick gestures, such as from the inside to the outside and vice versa, over the entire or partial sensor areas. The user is then able to perform input commands, such as “open application,” point, click, zoom, scroll, mouse-over and many others, without the need to touch the device.
If the design requires a specific gesture that is not included in the suite, Microchip provides near-term a gesture recording and training module that allows design engineers to add their own gestures to the library. Due to the MGC3130’s flash architecture designers can download the recognition parameters for these new gestures into the IC.
Furthermore, approach detection is a programmable function that scans for user activity while the chip is in self-wake-up mode. If real user interaction is detected, the system will automatically switch into full sensing mode while alternating back to a very low power self-wake-up mode once the user’s hand will has left the sensing area.
Flexible Adaption to the Environment
GestIC technology operates with a carrier frequency of around 100kHz. Whenever noise is detected from devices such as motors, inverters, chargers and fluorescent-lamp drivers, the MGC3130 automatically adapts its field emission frequency to a noise-free channel in the range between 70 and 130kHz, thus avoiding RF interference and providing a very robust solution.
On the other hand, its emitted energy is very low. This means that GestIC technology doesn’t cause interference with other systems, elements as evidenced by the fact that it passed EMI tests, such as the IEC 61000-4-3. Furthermore, while the maximum current consumption of the MGC3130 IC is 70mW, the majority of its power consumption is needed for the interpretation, evaluation and classification of the disturbed electrical field signals—not for the emission of the electrical field itself.
The Story behind it
For more than 10 years, the Munich/ Germany-based company Ident Technology – which was acquired by Microchip Technology in 2012 and joined its Human Machine Interface Division (HMID) – has gained experience and know-how around the topic of using electrical fields, and it has filed numerous patents.
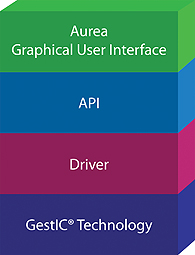
This know-how includes how to apply the theories of E-field’s in a real environment, the design of the sensing electrodes, the chip design, and the algorithms used to process the raw sensing data.
The wavelength of the 100kHz signal used by GestIC technology is roughly 3 km. This means that the dimensions of the sensing electrode area, which is typically less than 15 cm × 15 cm, is several orders of magnitude smaller than the emitted signal’s wavelength. This combination results in a very stable quasi-static E-field during operation that can be used for sensing conductive objects such as the human body, while the magnetic component is practically zero and no wave propagation takes place.
Enabling Future Applications
In order to facilitate application designs, Microchip’s HMID team is currently preparing a document that describes all of the relevant factors one must consider during the design and positioning of sensing electrodes. This will enable customers to design their own electrodes or implement them using materials already present in their designs.
Microchip also plans to offer a development kit named Hillstar, which is intended to support customers during the design-in phase. It features GestIC technology, including the Colibri suite, and connects to a PC through a USB interface, enabling engineers to conveniently connect their electrode designs and parameterize the MGC3130 chip on a PC.
Microchip’s feature-rich Graphical User Interface (GUI), dubbed Aurea, runs on the Windows 7 Operating System and provides control of the MGC3130’s parameters and settings, making it easy to update and save parameters (figure 4).
An informative video can be found here www.microchip.com/pagehandler/en-us/technology/gestic/gettingstarted.html#ooid=YzM2J2NjqvN4ridRUOLzUltg0_urPvxZ
For further details please check out the following Web page: www.microchip.com/gestic, while www.gesture-remote.com and www.gesture-cube.com provide inspiration regarding the capabilities of this new technology from Microchip.
www.microchip.com