Blood pressure monitors are no longer medical tools found only in hospitals and doctor’s offices. Automatic blood pressure monitoring is increasingly used at home. Home units are used not only by people who suffer from hypertension and need to track their blood pressure but also by people who want to monitor their health and get readings that are not affected by the anxiety or stress of a doctor or hospital visit. In order to keep units affordable for home use, system designers are looking for ways to maintain performance under stringent budgets.
Author:
Debbie Brandenburg, Product Marketing Manager, High Performance Analog Products at Exar Corporation
How they work
Blood pressure monitors use an inflatable air-bladder cuff and a pressure sensor to measure the air pressure in the cuff from which the blood pressure in the artery can be inferred. There are two numbers in a blood pressure reading, systolic and diastolic. A typical reading is 120/80 (systolic reading/diastolic reading). Many of today’s automatic blood pressure monitors work by first inflating the cuff with enough pressure to prevent blood flow. The pressure is gradually released until the blood begins to flow making the artery pulsate – this is detected as a small amplitude oscillation, at the heart rate, superimposed on the pressure reading. The measurement when the blood starts flowing is the measure of the maximum output pressure of the heart, the systolic reading. As pressure in the cuff is further reduced the amplitude of this oscillation reaches a maximum at the mean arterial pressure (MAP), which is when most blood pressure monitors also measure heart rate. After this the amplitude of this oscillation reduces as the pressure continues to be released until the cuff no longer restricts the artery. The pressure at this point is the diastolic reading, when the heart is relaxed.
Basic solution
A typical block diagram overview of a blood pressure monitor is shown below and a key element is the pressure sensor used to convert the pressure variations into an
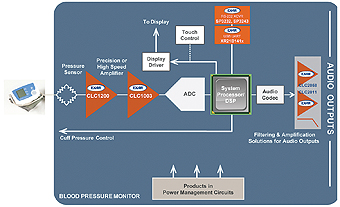
electrical signal. This is commonly achieved with a transducer formed from metal foil strain gauges bonded to a diaphragm. Pressure applied to the diaphragm causes it to deflect, which in turn physically deforms the foil of the strain gauge and results in a proportional change in its resistance. A Wheatstone bridge circuit converts this resistance change to a differential voltage for capture by the blood pressure monitor’s processor, via an analog-to-digital converter (ADC). As the output from the bridge is a small differential signal riding on top of a big common mode signal, an instrumentation amplifier is used to isolate and amplify the signal acquired from the sensor. A second amplifier provides additional gain along with band-pass filtering to remove any unwanted signals, such as slow varying AC components (due to movement of the cuff) and high frequency noise.
The processor at the heart of consumer blood pressure monitors is likely to be a relatively simple, low-cost microcontroller. More sophisticated units intended for professional use might employ a digital signal processor (DSP) and perhaps provide data-logging capabilities for longer term patient monitoring. As a minimum, the processor will need to provide the means for initiating the measurement process, acquiring the sensor data and converting this to meaningful blood pressure and heart rate readings that can be output to a display. These functions include controlling the pump that pressurizes the cuff and the valve that regulates the gradual release of pressure.
The user interface might comprise pushbutton switches and a simple liquid crystal display (LCD) although touchscreen displays are becoming more commonplace even in low-cost equipment. Audio output is not an essential feature for most blood pressure monitors but may provide a simple annunciator function to confirm correct operation and provide user feedback on the monitoring process. Data logging might be provided via serial I/O ports such as RS-232 or USB but could be enabled wirelessly using protocols such as Bluetooth, Wi-Fi or ZigBee.
Front-end implementation
Even the most basic of blood pressure monitors needs to deliver performance that meets recognized standards. The nature of the product also means that home users expect quality and reliability in an instrument that they can trust. But this doesn’t mean that designers have to cut corners or compromise on requirement specifications to achieve an affordable solution.
As discussed earlier, it is the design of the front end that determines correct operation of a blood pressure monitor, detecting the right moment to perform the measurements and capturing the pressure readings accurately. Clearly the specification of the pressure sensor is important but readily available, low-cost strain gauges, with precisely defined characteristics, can be matched with equally precise resistors to form the Wheatstone bridge circuit. With appropriate care this can be designed to balance out the effects of temperature variation and calibrated for initial accuracy
What then becomes important is the specification of the amplifiers and data converter that follow. Exar’s high performance analog product line offers a number of products that are ideally suited to the requirements of blood pressure monitors and offer a cost-effective solution. Firstly, its CLC1200 instrumentation amplifier is perfect for picking up the small signal generated when the balance of the Wheatstone bridge is disturbed by the slightest pressure variation sensed by the strain gauge.
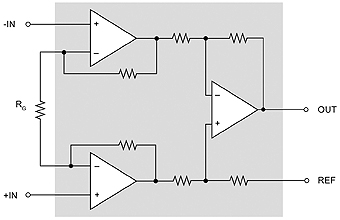
The CLC1200 architecture uses three operational amplifiers arranged in two stages: the differential amplifier stage provides a high input impedance, which avoids loading the Wheatstone bridge, while also rejecting the large common mode signal from the bridge’s DC bias circuit; the difference amplifier stage nulls the common mode signal and converts the differential signal to a single-ended output.
Exar’s CLC1003 single channel, voltage feedback amplifier provides all the necessary features of high gain-bandwidth, high slew rate, low noise and low distortion, to implement any band-pass filtering and additional gain that might be required in buffering the signal from the instrumentation amplifier and driving an ADC. It offers rail-to-rail I/O operation and extremely low THD (total harmonic distortion) of 0.00005%.
The final front-end component is the analog to digital converter itself. Here the key requirement is providing sufficient resolution to both detect the low amplitude oscillations from the pressure sensor that denote the systolic and diastolic measurement points, and to capture the mean pressure reading with the necessary accuracy. The actual ADC resolution required for a given design of blood pressure monitor will depend on a number of other design factors. This ADC is typically a 16 to 24-bit 100KSPS to 200KSPS Sigma Delta ADC.
The design of the analog front-end circuit used in blood pressure monitors and other medical diagnostic instruments is critical and plays a major role in the instruments’ accuracy and reliability. Exar offers several instrumentation and precision amplifiers to help system designers develop high-end hospital grade equipment as well as more cost sensitive home use models.
www.exar.com