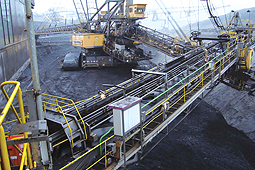
Every year, 20 million tonnes of lignite are excavated by the energy group Vattenfall using giant excavators. Robust computer technology delivers crucial information to ensure the excavators are operated as efficiently as possible and that coal performance is optimized. Vattenfall commissioned EWG automation GmbH to find an ideal hardware platform to renew the outdated diagnostic and visualization systems.
Kontron provided the fitting hardware solution.
The lignite open pit excavators in Welzow South in Eastern Germany have been in use for several decades. In the past, these were controlled manually. Today, more powerful diagnostic and visualization systems take care of increasing operational efficiency by monitoring, for example, specific flow rates and other key parameters. By applying the collected data, the excavator performance and the excavation angle can be adapted to the hardness and geological composition of the coal and so-called intermediate means (fault in the coal seam). Additionally, data regarding the motor currents and strains and the flow rates are sent from the measuring system directly over Ethernet connections to the operator’s workstation. Information on the specific coal performance is transferred to the mine control room and is also relevant for the surrounding power plants.
Continual improvements in the methods used to optimize operation logically mean that increasing demands are made on hardware. The technology for diagnosis and visualization no longer met Vattenfall’s expectations and an overall update was required. First, the systems had reached capacity limits due to the many functional extensions that were made. Therefore, the new systems had to deliver a higher performance level. Second, due to the range of extensions that had been made, the hardware structure had become heterogeneous with system components from a number of different manufacturers. Therefore, the hardware structure needed to be standardized so that maintenance and any expansions would be easy to carry out in future investments. Furthermore, the systems had to become manufacturer-independent. Vattenfall contracted EWG automation GmbH to develop this new powerful and standardized hardware platform, which also had to meet the high quality standards required in open mining. EWG had proven its expertise in numerous projects in opening mining and had carried out installations with guidance and control technology, software and special equipment development.
One system platform for many different requirements
Identifying the ideal platform where both the diagnosis and the visualization system could operate was the challenge for EWG, considering the requirements for both systems are very different. For the visualization of the necessary information in the operator cabin, such as status/error messages of the motors, only relatively average performance is required for good graphics as well as moderate hard drive and memory capacity. Diagnosis systems are completely different. Processing the large amounts of data regarding diagnosis, analysis and optimization of the individual technical processes, and the provision of fast status graphics based on complex data source, require a high level of computing performance. And for the assessment of the statuses, the user must have access to long term trends, which in turn requires extensive database archives. Consequently, increased demands are made on hard drives and memory performance. EWG had to find a common system platform that would be flexible and modular and that would cater for both systems.
High IO flexibility required
IO flexibility was essential, even though in most cases, Ethernet is used to connect operating clients. In order to guarantee maximum flexibility to the field, the system needed to support other interfaces such as RS232 ports or industrial IOs and field buses.
Deploying different operating systems and applications
In terms of software, the systems had to be extremely versatile as well. The computer systems on excavators are run on different operating systems and these are not always the latest versions, depending on how long ago the installation took place. Application software solutions from different vendors are also used. Consequently, this software diversity requires an open system structure that is capable of supporting all operating systems in different versions. A software-flexible system would also ensure that the migration to newer operating systems would be more convenient. New operating systems can be implemented gradually and if needed, old applications can be kept running.
Long-term investment security
Studying these requirements and recognizing the extremely long life cycles of mining equipment, it becomes apparent that in the mining sector, investments in process automation systems are long-term and the systems have to remain in use for several years. Therefore, it is important that individual components can be exchanged on a modular basis so that if a defect occurs, or an upgrade is necessary, entirely new systems do not have to be purchased. Given the long operating time of the systems it is also of paramount importance that the components have long-term availability. That means that not only the right components have to be selected, but the embedded computer standard itself must be chosen accordingly.
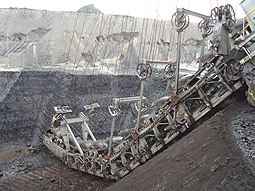
Low-frequency vibrations and dust
The best components are those that never need to be replaced. For that reason, systems were chosen which operate reliably even under the demanding environmental conditions of open pit mining. Even though most of the computing technology is housed in cabinet systems in a protected and air-conditioned environment, the systems have to ensure a safe start in all operating situations and under all conditions. The components are also exposed to a high degree of pollution caused by small amounts of dust from the ventilation systems.
Furthermore, the computer systems have to withstand a great deal of mechanical stress including low-frequency vibrations in the drive components in the 5Hz range. Non-directional impacts and shock loads must also be taken into account. Given these pressures and the required availability, the systems therefore have to be designed in an extremely robust fashion.
System evaluation led to CompactPCI
With this criteria, EWG started the search for rugged, industrial PCs, based on recognized industry standards and featuring flexible modularity. On closer examination, a large number of systems immediately failed the test. Only the CompactPCI standard remained as a candidate because of its robust construction and the fact that it has a wide range of IOs owing to its strong presence in the market. Due to its compact design, the 3U CompactPCI form factor makes space-saving system architectures possible that can be easily built into tightly-spaced driving cabs or control rooms. Choosing the manufacturer was the last step. EWG decided on Kontron. This was due to their positive experience working together on projects in the past: “Kontron’s CompactPCI products have shown very good voltage stability and strength. The products have also proven to be very robust and have delivered fail-safe operation even when temperature fluctuations and condensation effects have occurred”, Carsten Wetzk, Project Leader at EWG, comments. The systems have already proven themselves under mining conditions.
Service is crucial
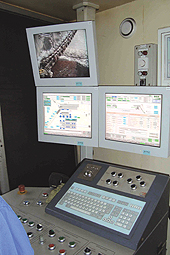
For EWG, a further important aspect played a major role. All components should come from one source and should be available as standard components. “Despite all the various possible options we had to choose from, more than anything we needed to find the right solution quickly,” EWG engineer Carsten Wetzk comments. “It was also particularly important to be able to obtain application-ready, pre-validated systems. That proves extremely practical and efficient. And it meant that we could focus completely on the integration of systems in the plant structure’s control system, which saved us a lot of time and ultimately saved the customer money.”
The system configuration
EWG’s configuration features a Kontron 3U CompactPCI rack system chassis. An integrated CompactPCI switching power supply and an external UPS take care of the non-fluctuating power supply and protect the equipment from damage by any voltages changes. The high performance 3U CompactPCI processor CP307 Intel ® Core(TM) 2 Duo processor with 2.16GHz, 667MHz front side bus and up to 4GByte of DDR2 SDRAM delivers the computing power needed for the measurement and visualization systems. In order to provide additional interfaces such as RS232 or PS/2, EWG opted for the expansion module CP307 CP307-EXT-IOID. Thanks to the soldered processor and soldered memory, the CP307 is equipped to withstand the continuous effects of shock and vibration which occur in mining environments. In particularly harsh conditions, hard drives are no longer implemented but SSD which has been tested jointly with Kontron and which has proven to be an especially good alternative.
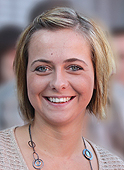
Autor:
Sandra Korsinek is product manager for 3U CompactPCI at Kontron
sandra.korsinek@kontron.com
www.kontron.com