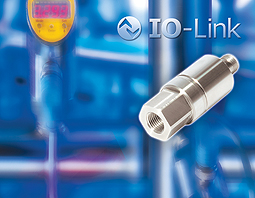
The new PC200 and PS300 pressure sensor family by Turck meets the requirements for hydraulics engineering.
by Thorsten Evers, Product specialist for fluid sensors at Turck Germany in Mulheim
To measure hydraulic pressure doesn’t seem to be a big challenge at first glance, but it is not easy to find the right pressure sensor for this application in the right range. Not every sensor can cope with the special requirements of the hydraulic industry.
Pressure sensors that are used for hydraulic systems have to meet specific requirements, but mainly they have to be very robust. Usually the hydraulic pressure is between 6 and 600 bar, but it is dynamic and not static. The constant alternating pressure not only strains the cells and the sealing material, but also the housing itself. It is important to choose the right combination of cell technology, sealing material and the sensor’s housing to ensure reliable pressure monitoring.
To resist dangerous pressure peaks that may exceed the normal operating pressure by several times over, the choice of the right cell technology is essential. Pressure measuring cells made of ceramic are approved for these kind of applications. They offer over-pressure capability, a good drift performance and a fast reaction time. Furthermore, ceramic is resistant to aggressive substances.
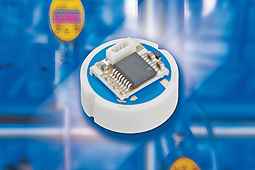
Because of these positive qualities, a measuring cell made of ceramic is the core of the new pressure sensor families, PC200 and PS300, from Turck. This piece of equipment processes the measuring signals directly from the cell and forwards them digitally to the evaluation electronics. The result is better performance when it comes to excess pressure, compared to standard ceramic cells.
High protection category IP69K
The pressure sensor is not only stressed by the hydraulic pipes, but also through outside influences like oil spray, mechanical forces or EMC influences. The PC200 and PS300 family (with display) are IP69K-rated for all areas of pressure measuring. The housing is made of special steel and the sealed control and display elements don’t allow moisture into the device. Further, mechanical forces up to seven joules – even on the display – don’t have any effect. Because of the new cell technology with integrated digitalization of the data, the PS300 achieves a high electromagnetic tolerance, as well as a high accuracy of 0.5 percent. The repeatability of sensors like this is mostly underestimated. Often, people look at the data sheet for the tolerance and the error information first, but what looks accurate at first may not be because temperature, hysteresis and other factors have not been considered.
The reason for inadequate repeatability often results from choosing the wrong material, which cannot guarantee the ideal interaction under pressure and temperature load changes. Naturally, the electronic components play an important role. Turck took this into account and made sure that the new cells had an improved repeatability by working on the signal processing. The signal is no longer analog but digital, which reduces interfering signals that occur through the development of extra-low voltage.
User-friendly
Product characteristics are not the only important factors; manageability is essential. This includes, among other things, enough space for the use of tools during mounting, sufficient access for the electronic connections and adequate programming possibilities. Turck built upon its PS400/500 pressure series in the new sensor family. A large, four-digit display shows the user the operating pressure, even through oily glass. The equipment is parameterized with two push buttons that are easily operated with gloves. A recessed push button needs to be pushed to confirm the changes with the parameterization; mistakes can be avoided with this safety feature. Optionally, the PS300 family can be operated according to the VDMA specification 24574-1.
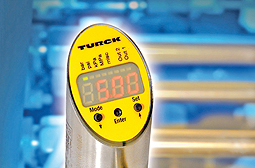
Until 15 years ago, mainly contact switches were used for monitoring pressure. These were reliable, but only to a certain extent. Higher requirements demanded by applications – like easily switching the units or reprogramming the switch points – made the electronic push button necessary. Today we face a change again: Better access to the instruments is needed to read the sensor data more easily. These days, a simple binary or an analog signal is not sufficient.
IO-Link in the future
IO-Link is the technological solution to these changing demands, and provides users with a standardized tool for the world of sensor technology and actuating elements. The technology offers new possibilities to make machines and systems even more efficient. The IO-Link technology is integrated into the PS300 sensors, so that users can switch to the IO-Link in the future and not at the present moment if they choose. If you talk about investment protection, you also have to talk about reliability and quality. A low price is tempting, but if there is a quality problem with the equipment it gets more expensive in the end, i.e. when there is a shutdown of a machine because of a low-quality sensor.
Conclusion
During the development of the PC 200 and PS300 family, Turck focused on quality and longevity of the product, as well as on the cutback of storage costs. The sensors with their robust, ceramic measuring cells and integrated digital signal processing show a considerable better performance than a standard ceramic cells. The two sensor families offer a device for all applications, and with the IO-Link the sensors adapt very quickly to different situations.
www.turck.com