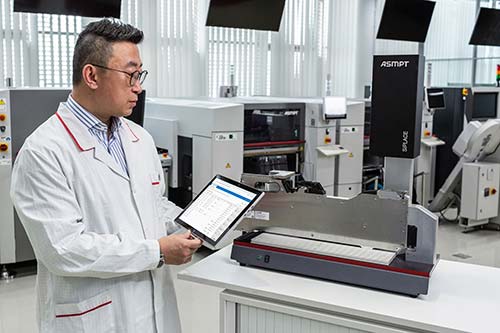
Factory Equipment Center continuously monitors the counters of all feeders in use on the shop floor. Once a preset number of operating cycles has been reached, the system locks the respective unit and e-mails a maintenance request to appropriately qualified employees. — Image source: ASMPT
In this age of Industry 4.0 and just-in-time supply chains, bringing the systematic maintenance of your production assets in line with your production planning is particularly mission-critical. Factory Equipment Center from ASMPT guarantees process reliability for machines, feeders, placement heads, nozzles, and other production assets on the SMT shop floor.
Today, suppliers in just-in-time supply chains can no longer afford any production standstills as reliably fulfilling delivery contracts and strengthening customer relationships have become essential prerequisites for the success of their business.
With ASMPT’s scalable Factory Equipment Center software for enterprise-wide asset and maintenance management, maintenance managers have a constant overview of the entire production inventory and can plan their maintenance operations automatically and error-free. Reliably supported by the software, technical teams can have sufficient manufacturing capacities in reserve at all times without building up service backlogs. Factory Equipment Center centrally manages the planning, time- and usage-based controlling, execution, documentation and support of maintenance and service operations for all production equipment, including machines from other manufacturers and non-SMT production assets.
To carry out maintenance operations, Factory Service Center supplies technicians with instructions, checklists and other information at the touch of a button. It also automates time-consuming reporting tasks. In addition, Factory Equipment Center knows the status and location of each piece of equipment and can visualize and monitor machine data.
“Factory Equipment Center is particularly useful when it comes to production-critical components such as feeders. In high-volume production environments with a wide range of products and many SMT lines, it is not uncommon for up to 15,000 feeders to be in use. With such large numbers of units, which may be spread all over the facility, maintaining an efficient inspection and cleaning schedule is a real challenge,” explains Eric Kirschner, Senior Product Manager at ASMPT SMT Solutions. “Factory Equipment Center keeps everything under control and ensures that our customers’ SMT lines run reliably and churn out products with maximum efficiency and productivity.”
Via the SIPLACE LAN and the WORKS OIB (Operation Information Broker) interface, the software scans the production environment and creates a comprehensive database of all connected assets immediately after startup. Once this has been done, it can automatically transfer the service schedules of all connected machines, feeders and other production assets into a central maintenance calendar.
The feeder maintenance journey
After collecting the initial asset data, Factory Equipment Center continuously monitors the counters of all feeders in use on the shop floor. Once a preset number of operating cycles has been reached, the system locks the respective unit and e-mails a maintenance request to appropriately qualified employees. This e-mail includes the exact location of the unit requiring maintenance and a list of all activities that need to be carried out. When a member of the maintenance team removes the feeder from the machine, the central maintenance instance in Factory Equipment Center is automatically notified.
The asset is subsequently tracked via automated racks such as ASMPT’s Active Feeder Racks, an electronic interface or via its barcode, which is scanned after each location change. In the maintenance area, the feeder is plugged into a test device, which triggers the cleaning process, for example. Once the feeder is operational again, the system reactivates it for use on the production floor. Each process step is automatically logged. Easy-to-read reports that meet the auditing requirements of contract partners can be compiled with a few mouse clicks.
New: Nozzle maintenance
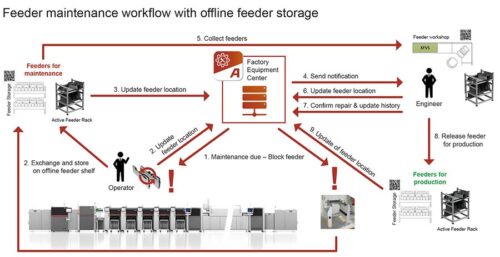
Complete maintenance cycle, using the example of a feeder: As a central management instance, Factory Equipment Center continuously controls and monitors the asset’s location and status – even if it is no longer on the shop floor. — Image source: ASMPT
With its new nozzle management capability, Factory Equipment Center can now also automate the maintenance of SIPLACE nozzles by reading each nozzle’s RFID tag on the machine’s placement head and including it in its time- and usage-based maintenance records. And since ASMPT’s networked machines monitor many other operating parameters, other events can also trigger a maintenance cycle, for example due to a significant increase in missed pickups or component discards.
Browser-based user interface and remote control
Via its browser-based user interface, Factory Equipment Center makes all its data available on a wide range of user devices at the entire location. A database of maintenance instructions provides quick guidance even to inexperienced maintenance workers. And for added convenience, the functions of ASMPT’s Remote Smart Factory solution are integrated into Factory Equipment Center as well.
Open Automation via a flexible licensing model
“According to the motto ‘As much as necessary, as little as possible’, Factory Equipment Center automates and optimizes the maintenance operations on the shop floor,” says Kirschner. “And true to our flexible and manufacturer-independent Open Automation concept, we offer a staggered licensing model for Factory Equipment Center with three packages: Essential, Plus, and Ultimate. This makes it easier for electronics manufacturers to get started, and they can expand their software at any time if needed.”
Online show: Facts on Open Automation
In the Facts on Open Automation show titled ‘Perfect link between production and maintenance planning’ airing on June 28, 2023, Laszlo Sereny and his studio guests will discuss how electronics manufacturers use powerful software to develop an agile and flexible planning strategy that enables them to react quickly to unexpected events and meet their goals in a dynamic environment.
For more information about Facts on Open Automation and to register, visit https://facts-on-open-automation.smt.asmpt.events/