You can buy more supply than you need, yet less is actually often better, says Don Knowles, VP Engineering at N2Power.
Just as it is important to properly size and specify your AC/DC supply, it’s also important for designers not to over-specify this vital component. It may seem counterintuitive, but “too much” of a good thing can have negative consequences in efficiency, cooling, overall product size, and even available vendors, besides the obvious downside of higher cost.
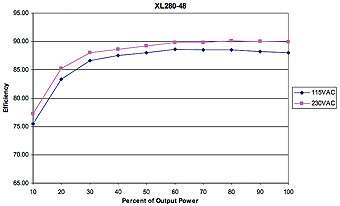
The first and largest factor to consider is matching the supply output capability to the load it must support. For example, if the maximum load (DC voltage × current) is 500W, then a 1000W supply provides much more design-margin insurance than you actually need.
What are the consequences of a supply that has so much headroom? The good news is that, obviously, you’ll have plenty of amps at the nominal voltage-rail values you need. Simple enough, end of story – but not quite. There are significant drawbacks to having all this extra, unused power available.
The biggest one has to do with inefficiency and its many consequences. Every supply has an efficiency vs. load graph, such as the one in Figure 1. For a well-designed switching supply, this efficiency is usually at its highest in the range of 80-95% of maximum rated load. [This general guideline does not apply to linear regulators and supplies, but those are unusual above fairly low power levels of a few watts.]
When operating at low loads, which may be most of the time in an application like a data center, the power supply can generate a lot of extra heat, and this is where the engineer’s nightmare of both obvious and unintended consequences starts. The obvious effect is that you are wasting more AC-mains power, so your system costs more to operate, and that cost is straightforward to quantify. The larger supply is also more expensive to buy, and it’s easy to put a cost number on that, as well.
But beyond those easily assessable factors are ones that are much harder to grasp.
As a consequence of the additional heat, which you must get rid of, you are now dealing with more complex design and budget issues related to convection cooling (which may no longer be possible), fans, airflow layout, and heat sinks.
These alternatives add direct cost, materials, unreliability, and constraints on packaging and layout to the design, and even limit your degrees of freedom as you need to squeeze more into the product box, or make the box bigger. In addition, the larger-capacity supply has a larger footprint, with clear negative consequences.
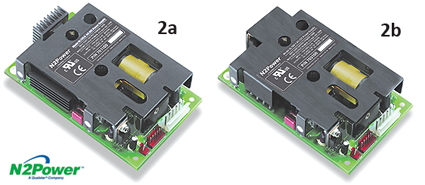
Further, as you select larger supply sizes, you’ll likely find fewer vendors to choose among, and fewer direct alternatives or second sources to your primary or preferred source. This may not bother you, but your purchasing department or contract assembly source may be uncomfortable and even push back.
For these reasons, most AC/DC supply vendors offer a broad family with many similar units, except for capacity, so you can match the supply size to the load with little excess capacity. For example, members of the XL series of AC/DC supplies from N2Power are available with closely spaced 125, 160, 275, and 375W ratings.
Note that adjacent-rated units from some vendors often differ only in their power rating, but have the same physical size and connector, so you can “interchange” painlessly if it turns out your actual power needs are different than you anticipated, as the N2Power XL125 and XL160 photos show (Figures 2a and 2b); both have the identical 3″ × 5″ inch (7.5cm × 12.5cm) footprint.
Of course, it’s easy to say “just design to use less overall power, and then size the supply to the maximum load.” The problem is that for many designs, the ratio between the maximum (peak) load and the typical load is large; 2:1 or even 3:1 ratios are common. So you must size your supply for the peak load, but most of the time it is running at far less, and is in the inefficient zone.
There are ways to circumvent this problem, such as by using an auxiliary booster for peak loads, a supercapacitor, or other techniques. However, each of these brings new design problems of switching them to the load, and the overall response to load transients. Therefore, to avoid over-specifying, try to get the maximum load of the system down to as close as possible to the typical load value.
Beyond efficiency, what else?
Other factors to consider are operating temperature range, operation voltage range, line/load regulation, various types of protection, redundancy, and I/O.
Given your ambient operating environment and the cooling scheme you’ll be using, what operating temperature do you need on the supply? Certainly, a supply which is specified to operate at higher temperatures costs more – but perhaps that allows you to “get away” with reduced cooling requirements, so that’s a trade-off to consider. Don’t forget low-temperature operation, as well, if your application is one of those where your supply has to survive or even just start up below freezing.
What is the nominal value of your AC line (mains)? Do you need a supply for only 115VAC, only 230VAC, or a wide-range supply that handles both ranges?
As usual, there’s a tradeoff: in general, a supply for both AC values is slightly more expensive, but the extra cost may be worthwhile because you’ll be able to buy more of the single unit, and your stocking, inventory, and support costs will be lower.
More complicated is the tolerance you need around the nominal AC line. Does your supply have to work with a fairly modest ±5% swing, a mid-range ±10% span, or a wider variation of ±20% around nominal? Supplies which can work with more-poorly behaved AC mains, yet still maintain regulation within specification, are more costly, and you’ll have fewer suitable vendors. If you need to tolerate a wide mains tolerance, it may be less costly to get a separate pre-regulator to keep the AC line in a tighter range and then use less-costly supplies.
What level of output absolute accuracy, stability, and regulation does your system require? Most supplies have a factory adjustment for nominal output value, so the supply should be fairly close to specified output. But keep in mind that while stability and regulation vary from vendor to vendor, and tighter specs cost more, you may not need that performance.
The reason is that many AC-to-final DC-rail supply paths now consist of multiple stages, where the first-stage AC/DC converter feeds an intermediate bus converter (IBC) or point of load (POL) converter, not the final rail itself. These DC/DC converters provide the actual voltages the system uses, and they may be able to tolerate modest variations coming from the AC/DC supply to their DC inputs.
Nearly all credible vendors offer features such as overvoltage protection, short-circuit protection, and output crowbar. Some offer extra protection against extreme line transients, including lightning-induced spikes and surges. If you don’t expect these upset events, or prefer to protect the supply with external, discrete components, you can use a supply that meets basic industry-wide transient specifications, rather than one with greater protection.
Some supplies offer N+1 capability, where you can set up an array of supplies with automatic switchover in case one fails. If you don’t need this level of reliability, or prefer to use a single AC/DC supply, this feature is unneeded.
There’s also a trend, especially in larger systems, to have the supply report many of its operating conditions (especially various internal temperatures) back to a system monitor, and even change operating parameters under direction of a system controller. For applications that don’t require this level of supply/system interaction, don’t spend for the I/O port (I2C, PMBus, SPI) and related circuitry within the supply.
Whether you over-specify your supply due to lack of understanding of your system needs, supply parameters, or just to sleep better at night, there’s really no need to do so. As with most engineering decisions, you’ll be able to specify what you need and not more, once you understand the priorities of your project and its market, as well as the tradeoffs your choices bring to the design.
About the author:
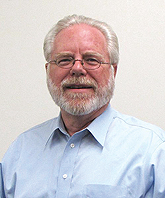
Don Knowles joined N2Power as VP Engineering 12 years ago after more than two decades’ experience in power electronics design and manufacturing spanning industrial, ICT and medical electronics sectors.
Prior to joining N2Power, he ran his own power electronics business for 20 years, designing power supplies and high-power AC and DC loads, and working with contract manufacturers. Don holds a degree in Electronics from American River College, Sacramento, California, USA.
www.n2power.com