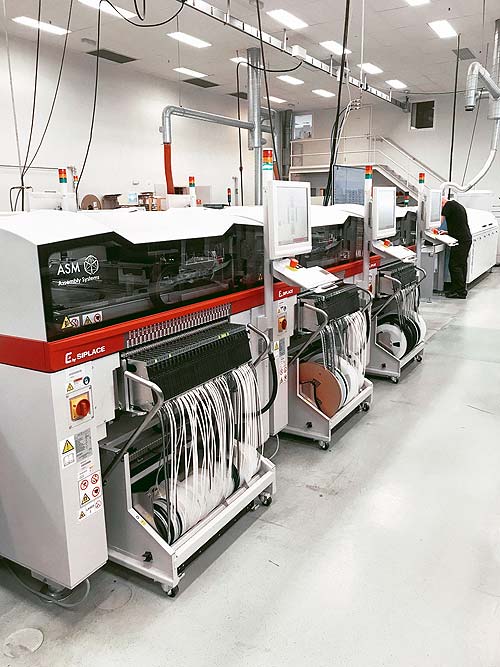
With the three E by SIPLACE placement solutions, setup times of up to three hours have been reduced to just a few minutes. — Source: ASM
When the growing demand for smart-home solutions had pushed Norwegian manufacturer CTM Lyng AS to its capacity limits, the company decided to transition to an integrated smart factory with E-Solutions for printing and placement as well as with ASM software solutions. The result: much more throughput and improvements in flexibility and productivity.
Business is good for CTM Lyng AS. The financial crisis of 2008/2009 had hit the pure-play EMS provider hard, which is why the company decided to make its own products in addition to offering manufacturing services only. This step and a successful merger brought the company back on the road to success. CTM Lyng has posted steadily rising sales ever since, has become a leading supplier of smart-home solutions in Norway, and today sells more than 300 products under its own brand.
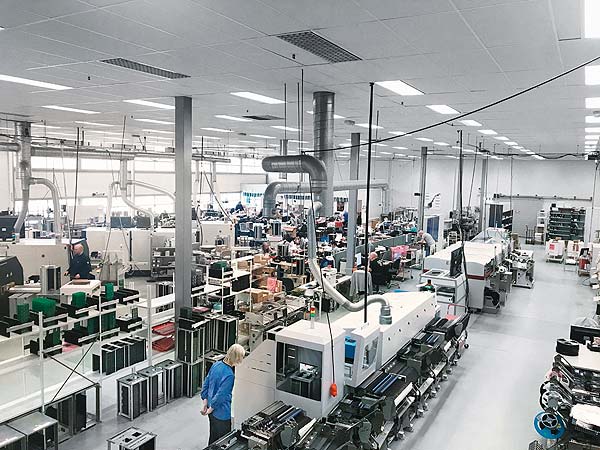
At the new production line with ASM equipment, CTM Lyng produces products under its own brand and new developments. — Source: ASM
Time to embark in new directions
“After our production had moved more and more toward our own smart-home solutions, the time had come in 2018 to make the necessary replacement and expansion investments,” explains Thomas Kruksve, process engineer at CTM Lyng. “Both production lines had reached their capacity limit, and our technical capabilities were no longer in line with the high demands we place on our products in terms of quality and flexibility.”
Another goal was to modernize and automate wherever possible the Norwegian company’s material management operations with powerful hardware and software solutions. “Our operators handled the material management and production planning more or less by the seat of their pants in processes that had grown over the years, which made the workflows increasingly susceptible to mistakes, depending on specific people, and more labor-intensive as the number of products and variants increased,” adds Thomas Kruksve.
ASM impressed with an innovative total package
CTM Lyng compared proposals from various equipment suppliers in detailed evaluations. “We wanted a mid-speed solution with short setup times and optimized material supplies that would give us the flexibility we needed to produce the PCB for our various product lines. ASM quickly was at the top of the short-list with its E-Solutions for printing and placement. We were particularly impressed by the software concept, because the E-Solutions software is identical to the software for ASM’s high-end solutions, which makes it compatible with their workflow solutions. In combination with forward-looking solutions like the ASM Material Manager and ASM Remote Smart Factory, the total package was unbeatable in terms of cost, effective benefits and investment protection,” says Kruksve.
Optimally positioned
ASM implemented at CTM Lyng one E by DEK printer and three E by SIPLACE placement machines. To supply the production with component reels, an automatic ASM Material Tower storage system is available. Material-related processes and setups are coordinated via the ASM Material Manager software solution, which closed the software support gap between the ERP and the shop floor.
“The new ASM equipment provides us with complete control over all aspects of the PCB production for the more than 300 of our own products,” says Thomas Kruksve. “From small batches to lots sizes of between 2,000 and 4,000 units we now produce exactly based on demand and with a level of speed and quality that we could never achieve in the past. The teaching and simulation processes for new product introductions are also impressive and accelerate the entire NPI process. And the new setup and material supply concept has cut our setup changeover times from several hours to a few minutes.”
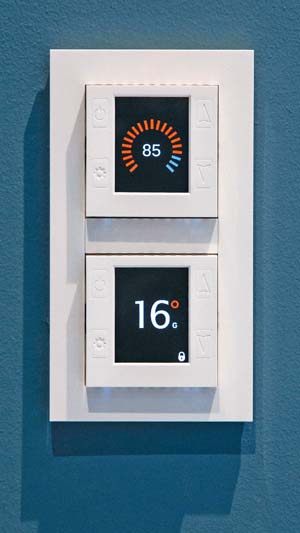
SmartHome control panel Microsafe mTouch One: Menu operation and temperature display are on a configurable colour screen. — Source: ASM
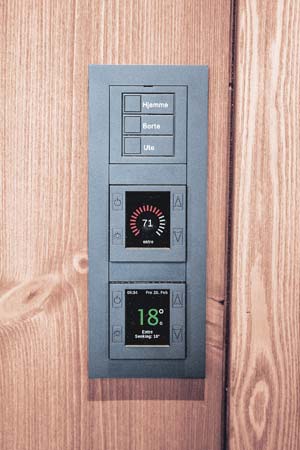
Microsafe mTouch energy saving switch: Wireless control device for one or more devices. Can be operated as thermostat, light dimmer or in combination. Different profiles are available: At home, absent, outside, day or night. (Shown in combination with Microsafe mTouch One) — Source: ASM
Significantly faster setups
For example, on the old production lines of CTM Lyng, setup changeovers lasting two to three hours were everyday occurrences – time that was long and unproductive. With the ASM Material Manager and a new family setup concept of the ASM E-Solutions, the setup times dropped to as little as one to five minutes, with 50 different products run on the line. “These are numbers that deliver previously unthinkable benefits,” says Kruksve.
Support is also provided by the ASM Line Monitor, which pools all production-relevant material status information and displays it above the line and on all station computers. Order and line status data is now available at a glance. The software prioritizes all pending steps on the lines and alerts the line with plenty of lead time – for example, whether a new component reel is needed or the remaining units on the reel are still sufficient to complete an order.
Material management optimized and automated
The installation of the ASM Material Manager and the ASM Material Tower led to significant changes at CTM Lyng. “The introduction of workflow solutions required our employees to change their way of thinking,” explains Thomas Kruksve. “ASM helped us to accomplish this with professional training that alleviated their initial reservations and demonstrated the advantages of automation and showed them how to deal with it. Today we all benefit from having an accurate overview of what is where on the shop floor. And the fact that the machines trigger material issues by themselves and notify the operators in advance of what needs to be picked up and installed where is a huge improvement for us.”
Secure access to ASM service specialists
To enable ASM’s service specialists to provide support for CTM Lyng’s operators and technicians at any time, the company also decided to install ASM’s Remote Smart Factory solution that connects all ASM line components and systems in a remote service LAN that’s separate from CTM Lyng’s corporate network and even has its own internet link. When problems occur or settings need to be improved, ASM service technicians can now access the machines directly and instantly. And if manual actions are needed to troubleshoot or optimize a machine, the ASM specialist can be consulted via video link and give the local technician step-by-step instructions. “They can access our machines only if we request it, and all activities are logged in detail. These links, which meet our strict security standards, have been very useful several times already, and always quickly and very efficiently,” says Kruksve.
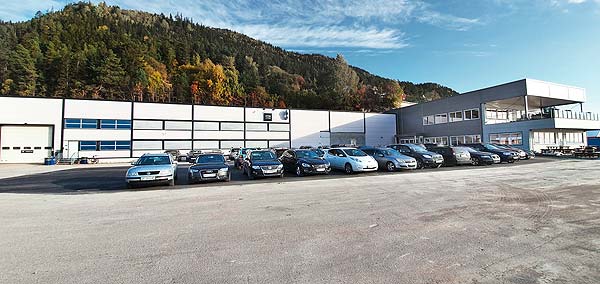
The company‘s headquarters in Vanvikan at the Trondheim fjord in Norway – high tech in picturesque surroundings — Source: ASM
Conclusion
At this time, the new production line is reserved for the company’s own brand-name products and new product developments. Electronics manufacturing services are provided on the second line. “The impact of the new equipment and the material management system on productivity, flexibility and quality has exceeded our expectations,” says Thomas Kruksve. To further automate and improve its material management, CTM Lyng plans to invest in more ASM Material Towers. “To better implement our idea of a smart factory, we also want to bring the ASM solutions and our ERP system closer together,” says Kruksve.
CTM Lyng AS is considered Norway’s leading provider of smart-home solutions in the areas of security and comfort, energy management, as well as lighting, heating and furnace controls. The company also operates as an electronics manufacturing services provider and original equipment manufacturer with brands like Mkomfy, mTouch, Microsafe and Centrol.
In 2015, CTM Lyng became part of Addtech Nordic AB, a division of Sweden’s Addtech Group (Addtech AB), which has roughly 2,200 employees in approximately 140 companies.