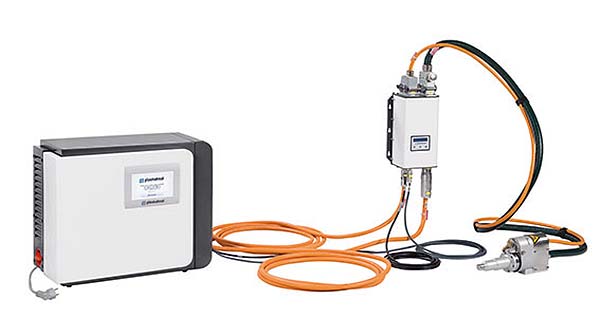
A plasma system includes the generator, the PCU (Plasma Control Unit) with the various monitoring modules and the plasma jet (from left to right)
In the age of Industry 4.0, process safety and reproducibility requirements are constantly increasing. In the automotive and electronics sectors, for example, or in medical technology, securing production steps and the traceability of those steps are important parts of documentation. Plasmatreat GmbH, world market leader for atmospheric plasma technology from Steinhagen, Germany, supports digitized manufacturing with its Plasma Control Unit (PCU) and makes numerous controls, regulation, and monitoring functions available to ensure consistently high surface-treatment quality and reproducibility.
One of the big challenges in surface treatment with plasma is that it must not leave visible traces on the substrate. So how is the result of the treatment evaluated? Auxiliary parameters such as purely inspecting the plasma beam’s color are not, in Plasmatreat’s 25 years of experience, sufficient for comprehensively evaluating treatment quality.
Highest Degree of Process Safety
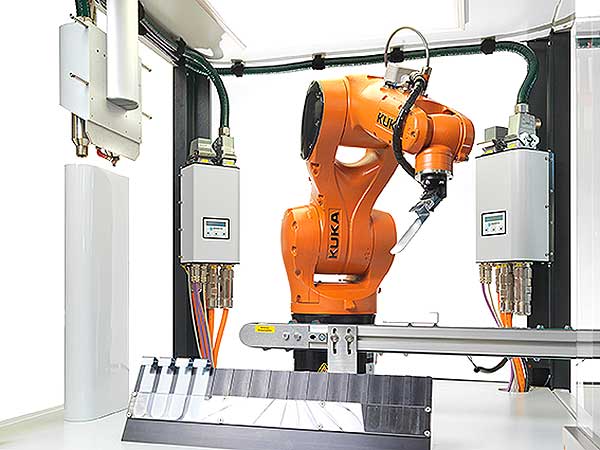
Individual manufacturing cells with automation solutions for seamless, process-safe integration into production lines are among the solutions Plasmatreat offers its customers.
The company therefore took it upon itself to continuously monitor the decisive parameters for a safe process, and developed the Plasma Control Unit (PCU). The various monitoring modules included in the PCU are, for example, the Plasma Power Module (PPM), which records power and voltage values directly at the jet head. The Light Control Module (LCM) provides ongoing documentation of the plasma generation. In addition, the Flow Control Module (FCM) continuously adapts the flowrate of the process gas to the circumstances. Functions like the Pressure Control Module (PCM) for testing jet back air pressure and the Rotation Control Module (RCM) for monitoring jet head rotation provide insight into the state of the jet head and the state of the motors, bearings, etc. when applicable. This means that data for predictive maintenance as well as production data are recorded continuously and support a smooth production process. Plasmatreat can guarantee that every component in a process is treated with the same plasma intensity and that the same quality is achieved in all manufacturing lines.
Suitable for Industry 4.0
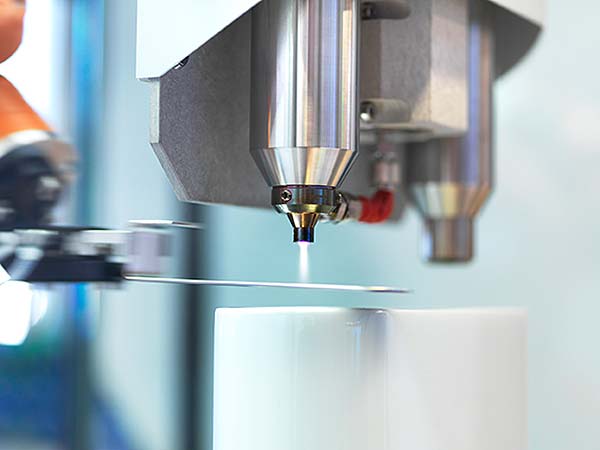
Openair-Plasma can be used for pretreatment of various surfaces, for example plastic, glass, metal or paper, in order to modify the properties of the surface for the subsequent process step.
Customers, then, can trust in Plasmatreat for data-supported quality assurance. All process data are made available in real time. The display integrated into the PCU supports the operator by providing an overview of the most important process parameters. In addition, it enables fast reaction times, since selected settings can be executed easily and directly on site. The process data can optionally be saved and are then available for later analysis and tracing. Thanks to this comprehensive control, regulation and monitoring of the plasma treatment, complete process control is ensured.
Easy Integration into Production Processes
With regard to Industry 4.0 use, the individual system components of Plasmatreat’s plasma systems (Plasma Control Unit and generator) are custom-tailored for use in intelligent process lines. They are connected via EtherCAT/CANopen gateways. The interfaces are thus defined in such a way that they can be used for different automation systems. Integration into existing manufacturing lines and network infrastructures is likewise possible. In addition to Openair-Plasma equipment for surface treatment, Plasmatreat also offers individual manufacturing cells with automation solutions for seamless integration into production lines. This allows the Plasma Treatment Units (PTUs) to be adapted to the customer’s process-engineering sequences and equipped with different handling options. Here, Plasmatreat solves the challenge of calibrating process automation to strike the right balance between efficient surface treatment and customized handling of components and groups of components, for example.