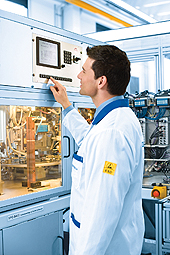
Whether for use in the open air, in machinery which experiences powerful vibrations or for continuous operation – PCs for industrial applications must satisfy requirements which differ from those for the consumer market. This is frequently a problem, particularly with respect to their memory components.
Author: Frank Bittigkoffer, Director Storage, Displays & Boards at Rutronik Elektronische Bauelemente GmbH
The majority of memory manufacturers produce their products for the end-user market, as this is considerably larger and less fragmented than the industrial market. The prevailing price pressure here, especially on hard disks and flash memory, ensures that memory is cheaper, but also that there is a steady decline in quality and ever shorter product life cycles with sudden product discontinuations.
Therefore, for all its components for industrial PCs, Rutronik relies exclusively on partners and products which explicitly address the industrial market. In this way, the customer can be sure of receiving components with long-term availability, sufficient strength and durability. If necessary, they can be supplemented by an expanded temperature range, 24×7 continuous operation, protection against aggressive gases or others. All Rutronik partners have comprehensive, clearly defined PCN (Product Change Notification) and EOL (End of Life) processes and universal RMA (Return Material Authorisation) handling.

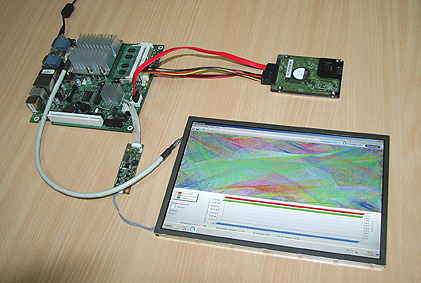
The industrial memories are available in all technologies and sizes, offering the perfect solution for every application. Hard disks are still a preferred medium on which to store data safely and for long periods of time. An interesting portfolio of products with high shock and vibration tolerances, an expanded temperature range, 24×7 operation and long data preservation is available from Toshiba, for instance.
Flash-based memory solutions are the first choice for applications which are exposed to stronger vibrations or shocks. However, intensive, knowledgeable advice is essential when considering these. For in able to remain competitive, the manufacturers must continuously lower their product costs. They use die shrinks and new flash technology to do this. However, these have a negative effect on the quality and longevity of the memory. For instance, TLC (Triple Level Cell) chips are increasingly being used in flash cards and USB sticks. It is only possible for data to be deleted from or written to these a maximum of 500 times. In comparison, MLC (Multi Level Cell) chips are able to accommodate 1000 to 10,000 write/delete cycles and SLC (Single Level Cell) chips approximately 100,000 cycles. There are also serious differences with respect to data preservation: While TLCs do not even store data reliably for one year, MLCs do so for a maximum of one year and SLC solutions for up to ten years. Even in industrial applications, customers frequently do not know exactly how large the data volumes are which are written to the card. However, the duration of the data preservation depends on this. Because corrupted data or even the failure of a memory may have fatal consequences, it is better to use at least an MLC-based or, even better, an SLC-based flash memory.
Firmware changes often bring unwanted surprises
The die shrinks also have another negative effect: Usually the shrinkage means that another controller must be used in the flash memory. This firmware change may have a major impact on the customer application. The memory may unexpectedly no longer function correctly or fail completely. According to manufacturer specifications, the new models are indeed frequently backward compatible, but this statement is based primarily on tests using boards from the major manufacturers and standard software. Customer using their own board or software should not rely on such statements.
However, the Rutronik manufacturers Apacer, Swissbit, Toshiba and Transcend do not just guarantee long-term availability of several years for their products but also a fixed bill of materials (BOM). This means that all flash memories are identical to the sample and each other. In the event of necessary changes to the firmware, the distributor receives a PCN, enabling it to inform all customers which are using the affected memory model. This gives the customer sufficient time to carry out tests using a sample of the changed component or the successor model to determine whether it will function correctly in its application. If this is not the case, the customer can reorder the outgoing component and evaluate alternatives in the meantime. Should the customer not find a replacement model, some manufacturers will even go so far as to test the relevant component in the customer application and adapt the firmware to it.
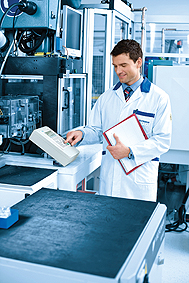
Individual kit solutions for industrial PCs
The Rutronik portfolio does not just include all industry-quality memory solutions but also all other components required for an industrial PC: Mainboards, displays, controllers, inverters, connection solutions, adapters, cables and power supplies. From these, the broadliner is able to put together individual kits to meet specific customer requirements within a short time.
The selection of boards ranges from industrial mainboards and single board computers, computer on modules (COM), PC104, blade computers, PICMG and backplanes, IPC and servers to box and panel PCs and HMI applications from manufacturers Advantech, DFI, emtrion, F&S, Fujitsu and Supermicro. Rutronik also has TFT displays and passive LCDs from Alpha Display, Displaytech, NLT Technologies, Sharp, Tianma and U.R.T. in its portfolio as well as touch surfaces from DMC and Hantouch. They also fulfil all the more stringent requirements of the industrial market.
There are no generally applicable rules for the selection, the applications are much too specific. The distributor provides comprehensive, manufacturer-neutral support here, contributing its experience gained from many customer projects. Initially, the selection focuses primarily on the available space, which determines the size of the board and display. When selecting the board, the required performance is also crucial. In addition, specific interfaces are available and other factors must be taken into account such as whether the PC must withstand very high or low temperatures or vibrations and whether it is designed for outside use.
Optimising cost and quality
The more requirements the component must fulfil, the more expensive it becomes. The objective here is to achieve the optimum compromise of costs and quality for the customer.
For instance, sometimes it is evident that the requirements of the board are not as high as specified and a more cost-effective alternative will be sufficient. Or that by utilising a slightly more expensive component, it is possible to do away with another completely, thereby reducing the overall costs.
As Rutronik stocks all components itself, the distributor can completely build and test the customer-specific system.
To this end, Rutronik keeps small quantities of around 90% of components in stock. Depending on customer requirements, the customer’s software is used in the tests or the hardware is tested at operating system level. Based on the test results, Rutronik is able to make any necessary alterations to the design. Consequently, the customer can be sure that the solution will function smoothly in practice, simultaneously saving a great deal of development time.
www.rutronik.com