With Smart Mobility ARChitecture, or SMARC™, SGET has ratified the first manufacturer-independent Computer-on-Module standard for purebred ARM/SoC designs. The specification was developed especially for Smart Mobility, with many stationary applications also profiting from these highly efficient SFF modules. While the standard has only just been published, already several modules and evaluation platforms, as well as starter kits, are available on the market. This means that OEMs can start right away on their application development.
by Gerhard Szczuka, Product Manager for Computer-on-Modules, Kontron
The new high-capacity ARM processors, as developed for modern smartphones and tablets, for example, impress developers with their high performance and low energy requirements. Thanks to these characteristics, manufacturers of long-term available, rugged industrial devices, machines and systems can implement solutions with these processors that they were not able to offer either with less complex ARM designs or with more capable x86 designs.
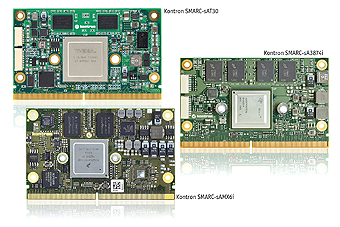
Consequently, a very attractive gap in the market has been bridged by making a comparatively large graphics and computing performance available in the lower single-digit watt range.
Thanks to the low energy consumption, fanless, rugged and extremely compact system designs are now possible. Heat removal is often just a question of connection to the enclosure But as a rule an optimized SFF design like this requires a highly integrated individual design. An approach is needed that allows manufacturers and mechanical engineers to integrate this new class of processors in their applications with the least possible design outlay.
Small form factor designs – ideally served with Computer-on-Modules
For this, OEMs require finished building blocks that allow them a high level of design freedom and the compactness of a full custom design while still effectively minimizing development expenditures and risks. Computer-on-Modules (COMs) take exactly this approach. They integrate the core components of a computer system such as the processor, relevant controllers, NAND memory and main memory on a highly integrated and and consequently compact COTS component.
The individual solution is designed via carrier boards to be developed in an application-specific fashion. They implement the signal lines from the module to the system interfaces and integrate additional application-specific components such as sensors or controllers. Carrier boards offer developers a particularly high degree of design freedom for their size and shape: only the minimum footprint is defined via the module size. Due to the very sophisticated design and layout of Computer-on-Modules, a carrier board is also noticeably easier and quicker to develop than a completely customized board.
Highly dynamic environment
With this modular approach, the module manufacturer alone shoulders the integration outlay for the processor. That makes Computer-on-Modules an ideal choice for efficient development of individual designs. Studies by IMS and VDC, from which you can derive an average annual growth rate of 25 percent for ARM-based COMs by 2016, show how big the need for such ARM building blocks is. This enormous growth will catapult the portion of ARM-COMs traded to just under 60 percent of the total COM market.
Following manufacturer-independent standards
In anenvironment as dynamic as this, it is important for developers to bet on the right horse. They should therefore give preference to COM solutions with manufacturer-independent standardization. Ultimately, they clearly offer more design reliability than manufacturer-specific modules. For long-term success, these standards should have especially broad support among the manufacturers. And it’s not just the small and medium-sized ones, but more than anything the big manufacturers.
All for one, but not one for all
One standard for all technologies however, is on the other hand not recommendable. Manufacturer-independent standards have to be designed in a consistent and focused fashion. However, too many options that are not compatible with one another dilute the enforcement of a standard. Special forms, interim solutions and hybrid functions should be avoided, wherever possible. But is there such a Computer-on-Module standard that focuses on ARM/SoC designs?
Recognized COM standards previously available only for x86 architectures
In the past, developers of ARM-based solutions had no support in the past under these conditions. Until recently, there was no Computer-on-Module standard adopted by an independent body that took the specific requirements of ARM/SoC processors into account. The existing module standards such as ETX® and COM Express®, which are the most significant COM standards worldwide, were developed for x86 architectures and are less suitable for ARM or SoC processor modules. The reason is that, due to the very different requirements for the power supply of the components and the sometimes very different requirements in terms of interfaces, it makes little sense diluting these standards.
New interfaces = new module standard required
Last but not least, ARM-SoCs also provide other interfaces than x86 platforms for similar tasks. MIPI interfaces are a good example for an energy-efficient display connection, and also the Serial Peripheral Interface (SPI) which is used for general peripheral connection,
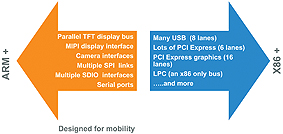
in contrast to Intel x86 where the SPI interface is only used for connection of a boot device. ARM-based processors also provide other specific interfaces such as I²S or – very important – various camera ports. So far they are not available in the x86 standard feature set. If you take all this into account, it becomes apparent that all known COM concepts that were originally developed for x86 processors and I/Os are not ideally suitable for ARM designs.
True module form factor
Subsequently, a purebred ARM/SoC-centered module form factor is required for ARM-SoC-based building blocks. The feature set should correspond exactly to these new processor generations and in addition should have an especially small footprint suitable for SFF applications. This means that developers do not have to compromise or take x86 conventions into account that are not relevant on ARM/SoC designs . Kontron has taken on this task and submitted a suitable module draft to the Standardization Group for Embedded Technologies (SGET). This draft has now been officially ratified.
SMARC™ – the new SGET standard
With ratification of the SMARC™ form factor specification, a dedicated standard for ARM-based building blocks now exists. SMARC stands for Smart Mobility ARChitecture. This architecture for ARM/SoC is characterized by extremely flat Computer-on-Modules and was almost immediately adopted by SGET.
That underlines both the great need for a new manufacturer-independent form factor standard and also the impact of the new group.
This new standard means that customers profit from a reliable roadmap with a high level of long-term availability which also ensures the reusability of their investments. This high reuse factor makes it possible for OEMs to lower their costs and ensure quick market launch times. And they are also manufacturer-independent. Basically, users get exactly what made COM Express® in the x86 world the most-used module specification: a standard exactly tailored to the specific requirements. It provides them with an extensive eco system of scalable products and services with which they can implement new SFF applications quickly and reliably and obtain a reliable migration path.
Slight depth and compact footprint
The SMARC™ specification describes extremely flat ARM/SoC-based, ultra low-power computer-on-modules. They define two module sizes: ‘short’ with 82 mm × 50 mm for extremely compact low-power designs and a larger one with 82 mm × 80 mm for possible future higher-capacity SoCs with an increased space and cooling requirement.
The proven and inexpensive MXM 3.0 plug connector was chosen as connector.
With its installation height of only 4.3 millimeters, especially flat designs such as tablets or wearable computers can be developed with an overall installation height that is less that one centimeter. On the electrical side, SMARC modules have a total of 314 pins. SMARC™ effectively provides 281 I/O signal lines. That is already 50 more than the old MXM 2.0 connector has altogether, for example. Consequently, clearly more dedicated interfaces can be specified as interoperable here. SMARC™ can thus support an extremely broad range of dedicated ARM and SoC processors, which also accommodates the heterogeneity of ARM processors.
Broad range of products from the very beginning
And since this concept impressed not only the initiator from the very beginning, the first product lines already became available at the same time as the ratification of the new SMARC™ standard.
OEMs can directly resort to a broad range of Computer-on-Modules and evaluation boards. Currently there is a choice of SMARC™ module families with ARM Cortex™ A8 or ARM Cortex™ A9 designs. The range extends from modules with the graphics-heavy NVIDIA® Tegra® 3 processor and Freescale’s especially broadly scalable i.MX6 family with single-, dual- and quad-core processors, all the way to the ultra low-power Texas Instruments Sitara™ AM3874. By taking a closer look at the feature set of these new modules, the bandwidth which it can cover becomes apparent.
NVIDIA® Tegra® 3 modules for graphics-heavy applications
SMARC™ modules on the basis of NVIDIA’s Tegra® 3 quad-core processor with 1.2 GHz and ARM® Cortex™ A9 architecture are oriented to image-centric applications for markets such as POS/POI, infotainment, digital signage, security and monitoring as well as medical and military technology. The integrated NVIDIA-GeForce® GPU makes these processor modules especially interesting. In conjunction with ARM it currently delivers the highest graphics performance for up to two independent displays.
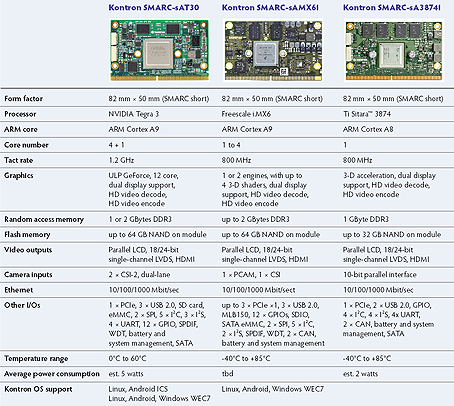
Among its outstanding performance features are HD video decoding, including MPEG2 and HD video encoding. In addition, they provide camera support via two dual-lane CSI-2 camera ports. Although they are based on the same processor technology as the highest-performance tablets and smartphones which are currently available in the consumer segment, they have the typical embedded long-term availability of seven years.
Freescale i.MX6 modules for highly scalable ultra low-power applications
Attractive graphics are also possible with the Freescale i.MX6 modules. But the versatility is – thanks to the high level of scalability – even more impressive. Their 800MHz ARM® Cortex® A9 performance ranges from single and dual to quad-core. This scalability offers the option of developing entire product lines that facilitate a differentiation from the entry model to the high-end solution just by means of the module used. They are oriented to intelligent devices that require balanced processor and graphics performance. Depending on the SoC design, they integrate one or two independent graphics engines with up to four 3-D shaders for life-like visualizations. A video decoder and encoder that can process videos up to full HD (1080 p) with 60Hz is also integrated.
Among the other advantages there is the above-average long-term availability of at least 10 years. In addition, the SMARC COMs equipped with this processor are developed by Kontron to work in the extended temperature range of -40°C to +85°C.
Ti Sitara™ AM3874 modules for energy- and cost-sensitive applications
The new modules based on the Texas Instruments Sitara™ AM3874 processor especially target cost-sensitive applications with the slimmer ARM® Cortex® A8 single-core design. Their extremely low power consumption makes them attractive and, thanks to the extended temperature range of -40°C to +85°C, they effortlessly brave the effects of wind and weather and are thus ideally suited for outdoor installations. Ti-Sitara™ modules support 3-D graphics acceleration and HD video processing. Two independent displays can be connected via 18/24-bit parallel LCD or 18/24-bit single-channel LVDS and HDMI. In addition, a parallel camera interface is integrated. At other interfaces, for example, 2 × SPI, 4 × I²S, 4 x multifunctional I²C and a dual CAN bus are supported.
Standard carriers and custom designs
Carrier boards for evaluation are also available for all these new SMARC™ modules. In accordance with the requirements of different ARM-based solutions for dedicated interfaces, they support various interfaces and various solid-state memories. But such a standard evaluation board could hardly meet the requirements of the individual SFF applications.
As a rule, an individual carrier board is required for the specific application. OEMs themselves can develop a fitting board design. But alternatively, most suppliers also offer the development of application-specific carrier boards; for example, selected sales partners of Kontron are in a position to offer this service. In addition, when larger quantities are required it makes sense to merge the module with the carrier into a full custom design. Most module manufacturers or their value-added resellers offer this too. However, the precondition for this is a suitable development team which also has the potential to implement the individual interfaces both on the hardware side as well as on the software side.
The second important building block – the software
A standard-based hardware offer is only one building block within the complex structure of a low-power SFF application. The second important question is: What about the software support? Due to the dedicated design of the ARM processors and the accompanying closer linkage of hardware and software, application developers likewise require dedicated software support. This is especially the case due to the fact that the new processors also represent a completely new processor architecture for some of the new applications. So what are the main considerations?
The operating system support first counts for software-side application development: which OSs can be used and is the specific hardware configuration supported?
Higher integration in the OS – BSP more and more important
Each manufacturer can only answer individually for its modules. Nonetheless, general requirement profiles can be established. In accordance with the purpose of the new SFF applications, primarily slim operating systems that can be compiled as needed with a small storage footprint are in demand. Above all Linux, the Linux-based Android and Windows Embedded Compact 7 are interesting.
VxWorks including Hypervisor, QNX and Greenhills are suitable for hard real-time applications. According to all expectations, subsequent Windows versions are also becoming interesting.
In contrast to x86 platforms however, an approach such as was taken with x86 operating systems is not possible on ARM-SoCs: first run the operating system and identify missing drivers so as to then successively integrate them.
With ARM technology, the precondition has to be created already in the boot loader through integration and adaptation of the drivers to support the dedicated processor platform and the required peripherals. This results in a noticeably greater significance and implementation outlay for board support packages than is the case with x86 designs. If OEMs integrate additional components via the carrier board that are not part of the standard equipment for these processors, then of course their drivers also have to be integrated in the boot loader.
Therefore, a comprehensive board support package is an absolute must for ARM-based modules. If the service of the hardware manufacturer would actually include driver porting of the individual components used on the carrier board, that would be a bonus. A software department has to be available for this. Then it can also offer direct support when adapting the boot loader.
New terrain: boot loader instead of BIOS
Where x86 technology relies on the BIOS, with ARM processors loading the firmware of the individual components is done via a boot loader. That indeed speeds up the booting process, but may be unfamiliar terrain for many OEMs.
If dedicated components are added to the carrier board, they likewise have to be integrated in the boot loader. And just as application-specific BIOS configurations are required, they also have to be created for the boot loader. Here, too, the question is open as to who can help if boot loader expertise is needed. Ideally, this range of tasks should also be covered by the hardware module manufacturer, since this is wherethe most in-depth knowledge of the system is.
More software services from the hardware manufacturer
Software services from hardware manufacturers are clearly gaining in significance. Customers should therefore make sure that the software department of the embedded hardware manufacturer is effective enough to also be able to implement these services. Many embedded manufacturers outsource these services.
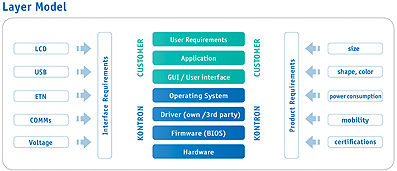
But from the customer’s perspective it is clearly more efficient if the customer receives this service from a single source, directly from the module manufacturer. Companies such as Kontron offer software support in-house for the most part. The company has more than 1,000 development engineers worldwide. More than two thirds of them work in software development.
Peter Müller says:
“With the publication of the SMARC™ standard for ARM/SoC-based computer-on-modules, the embedded market has all manufacturer-independent standards for all footprints and performance ranges that are required.
The leading form factors worldwide by far, ETX®, COM Express® and in the future SMARC™, are strongly differentiated but have clearly sharpened profiles and don’t cannibalize one another. Those are the most important success criteria for designs that are viable in the long term. Some solutions do appear to be generally well-crafted. But they run the risk of being crushed between the more clearly oriented standards. For this reason, we recommend that our customers pay heed to this straightforwardness and focus. Customers can in any case get every solution they need with ETX®, COM Express® and SMARC™. What more could you want?”
www.kontron.com