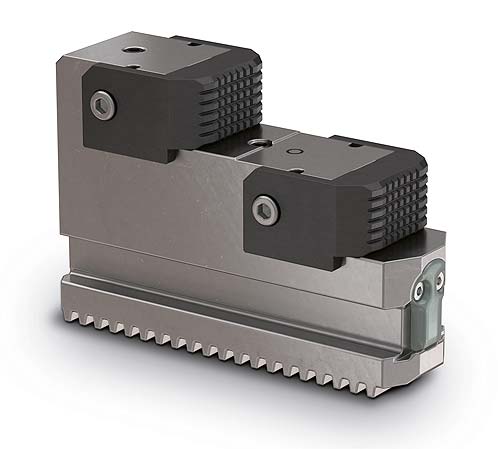
Figure 1: Measuring clamping jaw iJaw as a console jaw with exchangeable clamping inserts and two clamping stages
In Milan on September 30, 2021, the clamping technology specialist Röhm presented the iJaw clamping jaw for the first time at EMO 2021 in Milan. It allows the clamping force to be measured in real time during machining. Röhm thus solves a problem for which there has been no accepted industrial solution up to now: the clamping force is usually set by the operator of the machine tool and is a matter of experience. Errors during machining due to incorrect clamping force or workpiece loss are therefore preprogrammed. The iJaw presented by Röhm integrates sensor technology for clamping force measurement as well as wireless data transmission in a full-fledged clamping jaw. The measurement takes place directly at the clamping point to the workpiece; the data transmission to a gateway makes use of the upcoming industry standard IO-Link Wireless. The gateway can be connected to the machine control system via the integrated Profinet interface and/or sends the data to a cloud via the integrated LAN interface.
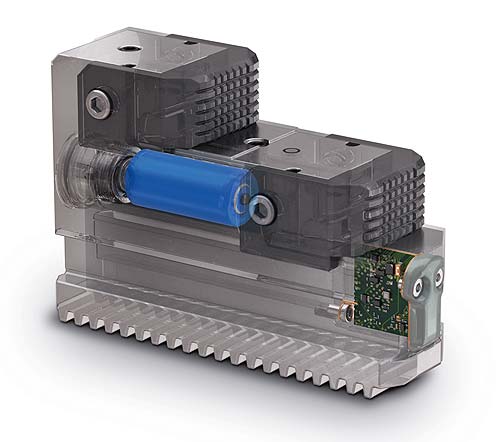
Figure 2: Sensor technology for clamping force measurement and electronics for wireless data transmission via IO-Link Wireless, as well as a rechargeable battery inside the iJaw
Even on the most modern machine tools, workpieces are clamped today in the same way as they were a hundred years ago: the operator clamps “by feeling”. Due to the lack of sensors, the machine tool can only support the operator to a limited extent. And to ensure that workpieces are really “securely” clamped—no one wants to risk ejection—the clamping force is often set too high. Especially with thin-walled components or sensitive surfaces, this quickly leads to deformation and crushing.
With the iJaw, the clamping specialist Röhm presented a clamping jaw with integrated sensor technology for measuring the clamping force directly at the clamping point. There is simply a clamping insert that is only a few millimeters thick between the sensor and the workpiece. Röhm thus eliminates almost all falsifying influencing factors and the iJaw can provide information about the actual clamping force applied to the workpiece. The iJaw transmits the measured data wirelessly to a gateway via the robust IO-Link Wireless protocol with a high sampling rate of 100 Hz. This means the iJaw measures in real time during machining. To this end, it has a suitably robust hardened steel and waterproof (IP 68) design. The transmitting antenna has a cover made of high-temperature plastic to protect against glowing chips. The iJaw can be mounted and used on all lathe chucks with a suitable (standard) jaw interface like any other clamping jaw. For the market launch, the iJaw is available as a stepped jaw for lathe chucks with straight or helical toothing in sizes 215, 260, and 315. Suitable lathe chucks from Röhm are the Duro-A RC, Duro-NCSE, and Duro-NC power chucks with the jaws quick-change system, as well as the counterpart from the conventional range, the Duro-T. To adapt the jaws to different workpiece geometries, there are various exchangeable hard and soft clamping inserts that are locked onto the jaw with screws.
Gateway as data hub
The gateway with the IO-Link Wireless receiver is used to receive the data and forward it. The gateway offers a Profinet interface for connection to the machine. Via this interface, the data is available at the machine control system and can be displayed on the HMI of the machine tool and/or further processed by the machine control system. The iJaw can be connected to the Internet via a LAN interface on the gateway, making it a true IoT solution. The data can be sent via this to a cloud where it can be archived and further processed.
Seven application scenarios identified
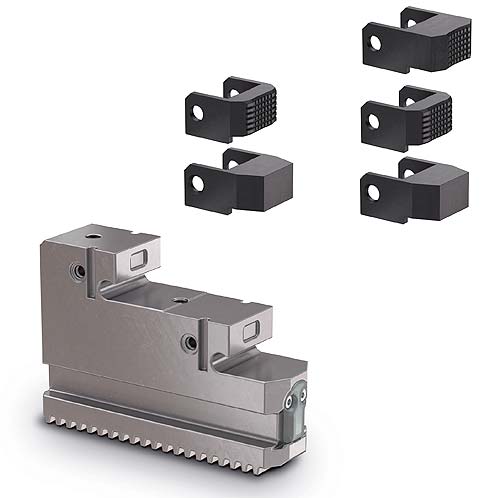
Figure 4: Different, exchangeable clamping inserts are available for the two clamping stages for adaptation to different workpieces
“We have identified seven very different scenarios in which the iJaw offers significant added value,” said Claus Faber, Head of Product Management and Marketing at Röhm. The first three scenarios are about the ‘feeling’ before and during machining. Before machining, the iJaw assists in feeding workpieces and setting up the clamping system. If errors occur, the measured clamping forces deviate from the target values and a manual or automated reaction can be initiated. During machining, clamping forces that are too high (risk of damage to the workpiece) and clamping forces that are too low (insufficient holding forces up to ejection of the workpiece) can be detected. Three further scenarios offer solutions for the evaluation of series and serial measurements. Here, changing clamping forces can be used to detect trends at an early stage. This includes the early detection of upcoming maintenance to maintain the clamping force or the wear of tools. Rejects can already be identified in the machining process, i.e. during their manufacture.
“In the last scenario, we mainly see documentation,” explained Claus Faber: “On the one hand, this is highly interesting for components requiring documentation—such as in aerospace technology—but also for product and process optimization tasks. If I want to know again after a longer period of time how a component was manufactured, I can research the manufacturing situation in the data in the cloud. The iJaw archives the fingerprint of the machining, so to speak.”
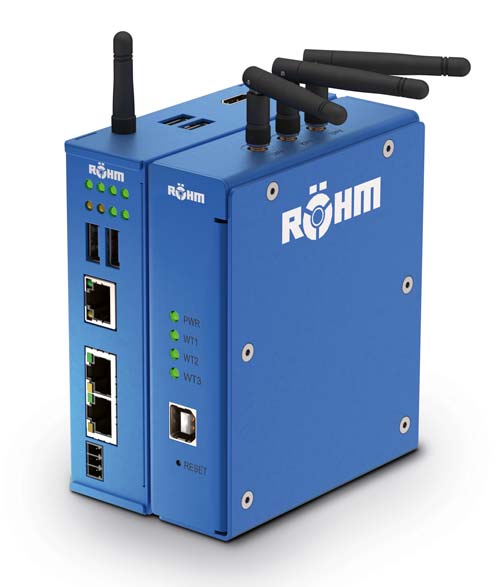
Figure 5: The gateway receives the data from the iJaw via the IO-Link Wireless protocol. Via Profinet, the data is available directly at the machine control system for display on the HMI or for further processing for process control. The data can be sent via LAN to a cloud and used for visualization, documentation, or analysis.
Claus Faber added: “But we are sure that there will be a multitude of other applications by our customers. We won’t even conceive of most of them in even the keenest brainstorming sessions.”
Development partners machine tool manufacturers DMG Mori, WFL Millturn, and EMCO
Since the end of 2020, Röhm has had an exclusive development partnership with machine tool manufacturers DMG Mori, WFL, and EMCO. They tested the iJaw on their machines in the final phase of development and accompanied Röhm to the series production stage. DMG Mori presented the iJaw to invited guests on a CTX beta 1250 TC 4A at the Pre-EMO in Pfronten from September 20–25, 2021. WFL presented the iJaw on an M50-G at the EMO 2021 show in Milan in Hall 4/Booth D09.
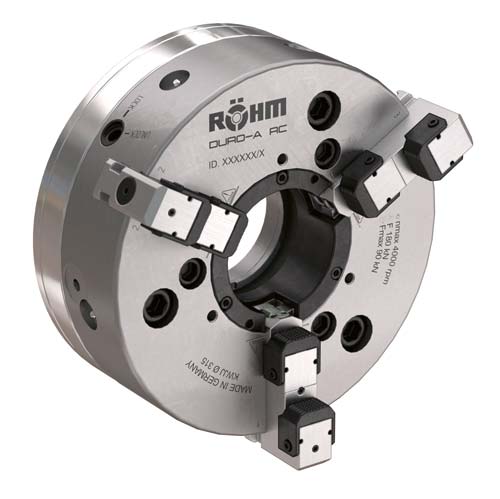
Figure 6: The iJaw fits on any lathe chuck with a suitable standard interface. The picture shows the iJaw on Röhm’s power chuck Duro-A RC with the jaws quick-change system.
IO-Link Wireless as an upcoming industry standard
Röhm sees the IO-Link Wireless protocol as the coming standard in wireless communication in the industrial environment. Compared to Bluetooth, which is widely used today, IO-Link Wireless is significantly more robust and stable. Röhm is convinced that IO-Link Wireless will become increasingly prevalent in upcoming IoT products. Röhm has therefore secured exclusive use for applications in clamping technology from IO-Link Wireless specialist CoreTigo for the development period of the iJaw technology. CoreTigo is a development partner for the hardware components for wireless transmission.
Presentation to the world public at the EMO 2021 in Milan
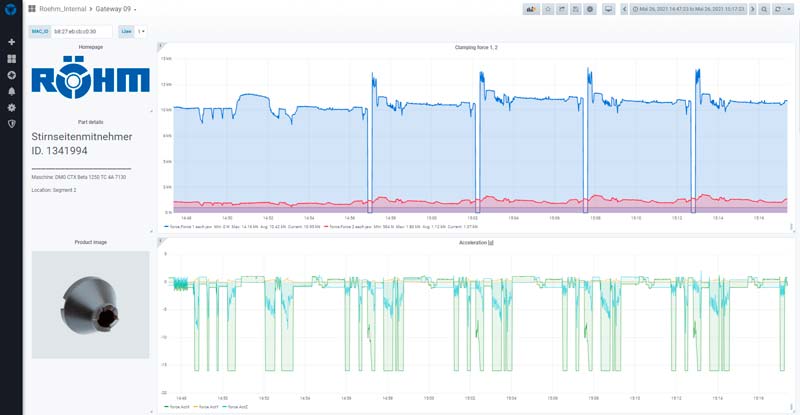
Figure 7: Manufacturing of face driver plates. The iJaw measures the clamping force at 100 Hz during machining in real time. The data is forwarded to the gateway and from there to the machine control system and/or a cloud.
Röhm exhibited the iJaw for the first time at the international metalworking trade fair EMO from October 4 – 10, 2021 in Milan. Interested visitors experienced the iJaw in action on a specially developed demonstrator. The demonstrator consisted of a power chuck with the jaws quick-change system of the type Duro-A RC in size 315 from Röhm. The measured data of the clamping forces on the jaw are transmitted to a monitor in real time. Visitors experienced the sensitivity of the iJaw when pressing on the workpiece because even such force effects are measured and displayed as clamping force changes.
The iJaw will be available as of February 2022.