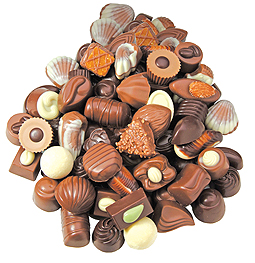
Informational advantage through RFID: Wireless identification of chocolate forms guarantees transparency during the whole production chain
Wireless identification via RFID creates an enormous potential for all production processes. The technology finds its way into more and more processes. The RFID solution becomes thoroughly efficient if used during the whole supply chain of a production process, for example through the identification of forms during the production of chocolate.
Dark chocolate, milk chocolate, white chocolate, with nuts or praline, shell-shaped or a truffle – the possible forms of chocolates are as numerous as the preferences of the users. Confectionery manufacturers usually offer different products, which means flexible production processes: different casting moulds are needed, new loads need to be inducted into the manufacturing plants and be replaced or cleaned during the production process.
The efficiency of industrial large-scale production depends on the availability of all components along the production chain, especially with flexible production processes. Information about the production steps is essential. For the sub-processes involved in chocolate production, wireless identification (Radio Frequency Identification) contains enormous automation potential – and improves plant efficiency and safety at the same time.
Opposite to customary auto-ID procedures, like bar or data-matrix code, robust wireless identification solutions like the BL ident RFID system from Turck offer an advantage for confectionery manufacturers. The electronic data medium (tag), as well as the combined read-write heads that are necessary for the data transfer, work reliably under the difficult conditions of the food production – neither increased temperatures nor pressure, cleaning supplies or moisture can harm the components. The contact-free, fully automated data transfer between the tag, combined read-write head and controls allows a continuous tracking of the goods and the forms through all steps of the production process. With an RFID system that is compatible with this specific process chain, every step of the supply chain can be monitored, recorded and traced back.
Teamwork for RFID
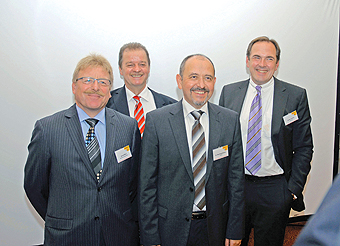
To meet the specific requirements of the chocolate manufacturers, Turck cooperates with the industry giants Winkler
and Dünnebier, producer of confectionery machines; Hildebrand, maker of cleaning systems; and Agathon, the manufacturer of forms. The common goal: To understand the requirements of the production chain and to offer a trade-specific solution for confectionery manufacturers.
The solution that combines the knowledge of the different industries has been met with interest by more and more chocolate manufacturers. Among other things, the four project partners presented the results of their cooperation at a workshop at the SPS/IPC/Drives show. Representatives of known chocolate manufacturers caught up on the practical saving and optimization options a RFID solution offers.
Constant identification
For constant identification of the chocolate forms throughout the entire process, the producer of the forms equips them with robust RFID tags. This allows the different forms for the numerous end products to be identified easily and anytime – even when stocked. The data of every single form is available centrally, so stocking procedures can be carried out without having to count the stocked forms manually at high personnel costs.
During the production process, the tags allow the backtracking of every single form – up to thousands of forms can be at one plant. Combined read-write heads at the loading stations, the casting machines or important checkpoints, record and forward the saved data to the controls. The operating staff knows at anytime at which point of the production process the forms are in and what their current status is; for example, if they need to be filled, if they have received their content, if they are cooled down or if they have finished the whole production process and are ready to start the cycle once again. This information helps to organize the load changes more efficiently and avoid plant downtimes – the whole production cycle is monitored in real time and disturbances are discovered immediately.
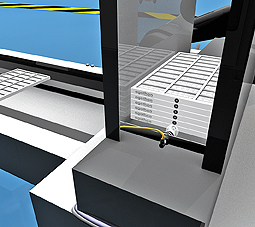
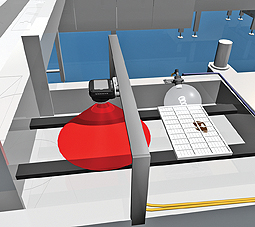
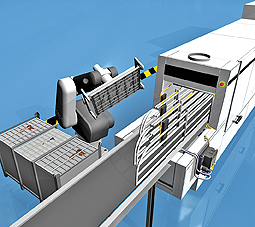
Chocolate forms that are damaged or contaminated are easily identified through RFID and can be removed from the production process and sent directly to a connected cleaning plant. The special RFID tags and combined read-write heads from Turck even withstand wash-down environments. Thanks to the modular RFID concept with robust tags (up to IP69K), combined read-write heads, food and beverage compatible cables, and fieldbus and interface components, Turck’s BL-ident system can be easily integrated into difficult environmental conditions and preexisting automation structures.
Identification with additional value
Wireless identification offers more advantages than the identification of intermediate or end products or product carriers. The EEPROM or FRAM memories, with capacities up to multiple kilobytes, record production dates or cleaning times that are saved with the identification numbers (Unique IDs), so guidelines of hygiene and quality can be monitored. Also, automated procedures, like the loading of the casting machines or the precise placement of the products or product carriers close to handling robots, can be carried out reliably with a RFID system. Last, but not least, the forms that have to be replaced because of contamination or material defects can be identified and ejected immediately before they lead to faulty end products.
Safety creates efficiency
Because all of the relevant data is written onto and read-out from the RFID tag automatically, the plant operator doesn’t have to enter the data manually and has the updated data of the production facility. The waiving of manual input and controls doesn’t only minimize the direct operating costs but also the follow-up costs that are caused through plant downtimes. The automatic data transfer opens up a lot of new automation potential, because of the applicability along the whole production chain. It provides a comprehensive and flexible tracing system that is easy to integrate and upgrades the production safety and the plant efficiency. Despite the numerous intermediate products, product carriers and handling processes, the manufacturers can survey their whole production with a few mouse clicks – according to EG-Guidelines for the food industry.
Author
Dr. Bernhard Grimm is the industry manager for the food and packaging industry at Turck in Mülheim.
www.turck.ro