For environmental monitoring of agricultural areas, researchers at CTR Carinthian Tech Research AG have developed an imaging system with multi-spectral data analysis that is integrated into a UAV (Unmanned Aerial Vehicle). For data recording directly in a UAV, CTR required a shock- and vibration-proof embedded computing platform that must be especially light and compact for the use in drones.
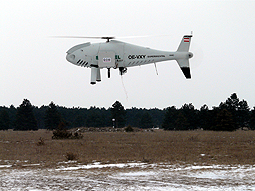
UAV-based environmental monitoring with Kontron Embedded BOX PC as a data logger
For the optimization of crop yields, it is essential to carry out an analysis of soil and vegetation. These data must record, for example, the ground water status and nutrient content of the soil or pest infestation.
This must be as up-to-date and accurate as possible, in order to respond quickly and precisely. Small fields are mostly maintained through personal sighting and manual soil sampling. For larger agricultural areas, however, this is very time consuming and costly and also not very accurate, since only isolated samples can be drawn.
Thus, the greater the agricultural area, the greater the need to obtain these measurements more efficiently.
Environmental monitoring with multispectral imaging
An alternative for the data collection is the environmental monitoring from the air, for example, by aircraft or satellite. The advantage to this is that with the help of aerial photographs, large areas of land can be recorded and analyzed in a short time. This is especially effective if you combine the digital image recording with spectroscopy methods. With this you can determine, for example, how much energy a plant reflects or absorbs in the form of photons or electromagnetic waves. Green plants reflect, for example, relatively little red light (wavelength of about 600-700 nm) in the visible spectral range, but in the infrared range (wavelength of about 650-1100 nm) relatively much. In addition, the reflection in the so-called “near” infrared range (in the infrared range, this lies close to the portion of the light that is visible to the human eye) strongly correlates with the vitality of a plant. The healthier a plant is, the greater the degree of reflection in this spectral range. Compared to conventional aerial photography, in which one can recognize only forest, water, or open areas, multispectral image processing offers the opportunity to identify whether plants need water or nutrients, or whether they are being attacked by pests. Other application fields lie in geology (rock analysis) and in environmental monitoring (detection of oil pollution, hydrological studies, and risk management).
To perform such multispectral measurements, the light must be refracted through a prism into the required wavelengths and recorded by special camera systems. Such camera systems are used for example in satellites that continuously collect data worldwide, such as global climate change and the resulting changes in vegetation. However, these satellite data are difficult to access and are only rarely available to farmers for any particular desired date. Therefore, aircraft are also used for current image data acquisition, which is very costly, however, and for European farmers only worth the expense in the rarest cases, namely for very large agricultural land.
But a more cost-efficient and environmentally friendly solution provides the image data collection with the help of a drone – a small unmanned flying object, which is radio-controlled from the ground.
Five image channels in one fell swoop
For use on such a UAV, the researchers at CTR have now developed a new imaging system for multi-spectral data analysis for three image channels in the visible wavelength range (400-500nm, 500-590nm and 590-670nm) and two image channels in the near infrared range (670-850nm and 850-1000nm), which can record and automatically analyze them. The system was integrated into the UAV (Unmanned Aerial Vehicle), a CAMCOPTER® S-100 from Schiebel, and successfully tested in flight operations. The innovation of the new CTR system is such that, in contrast to previous hyperspectral image acquisition methods, for the first time a multi-channel camera system by Quest Innovations is used.
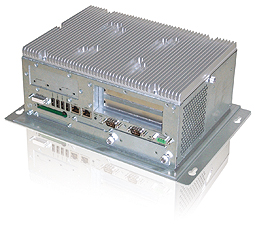
The advantage of this camera design is that all five image channels are recorded simultaneously and capture exactly the same image, so that the post-synchronization of the five image channels is no longer necessary, eliminating the need for enormous computing capacity and complex algorithms, and thus saving costs. This is made possible by the use of common optics for all five CCD sensors. The camera resolves to 1280 × 1024 pixels per sensor, giving a particularly high spatial resolution at an altitude of 150 meters of 10 square centimeters per pixel (for comparison, airborne systems offer a spatial resolution of between 2.5 to 10 meters depending on the altitude). The frame rate of the camera is 30 frames per sensor per second, which with five CCD sensors, corresponds to a data rate of more than 210 MB per second. In operation, only one employee is needed to control the drone from the ground.
High requirements for the hardware
For reliable recording of the high data volume during the flight, CTR required a suitable embedded computer system that could be integrated directly into the drone. “For use in the drone we needed PC hardware which must be powerful enough to handle the data stream of more than 210MB per second without problems. Second, for use in the sometimes harsh environment inside the drone, it must also be particularly robust and shock-resistant. For use in a UAV with a limited payload, the hardware should also be as compact and lightweight as possible and easily accommodated in a sealed enclosure,” says Martin De Biasio, Project Manager at CTR. “In Kontron’s product portfolio, thanks to the comprehensive advice regarding next systems, we very quickly found what we were looking for. Especially advantageous was the fact that our desired system was already available as an individually configurable standard product, eliminating the burden of adaptation and thus significantly reducing the time-to-market.”
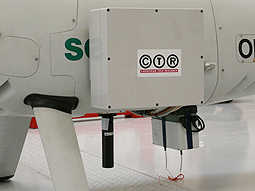
In the end, CTR decided on the Kontron V-Box Express II, which was offered by next system Vertriebsges.m.b.H. as Exclusive VAER (Value Added Embedded Reseller) for Austria. This modular Embedded Box PC is extensible via both PCI and PCI Express standard cards and integrates as a processing core an ETX express Computer-on-Module. This conforms to the PICMG® specified COM Express® standard, which benefits CTR in long-term design security and scalable performance. Additionally, these Computer-on-Modules are available in various performance classes, which can be swapped out easily with each other. If more performance is required in the future, then it is sufficient to exchange the Computer-on-Module with a more powerful version with the latest processor technology. CTR obtains additional design security through the long-term availability of the Kontron system (up to 5 years), but also by the high system availability thanks to its high MTBF (Mean Time Between Failures) of more than 40,000 hours. In addition to the energy efficient fanless design, the system features shock and vibration resistance (IEC 60068-2-27 and IEC 60068), which Kontron ensured through extensive testing procedures in the development and production phase. Next system also provided the configurable system for CTR with a particularly robust SSD (Solid State Drive) as data storage medium. And thanks to the V Box Express II’s available PCI-Express slots, the framegrabber card could also easily be integrated with the multi-channel camera system. CTR has also benefited from the compact size of the V Box Express II (235 × 330 × 130mm), for it allowed the computer to be easily attached to the drone, without negatively affecting its flight characteristics. Important in this context was also the high energy efficiency of the Box PC, which allowed it to be passively cooled and thus easily mounted in a sealed enclosure on the drone.
Authors:
Ingrid Hildebrandt is HMI Product Marketing Manager at Kontron
Martin Schiller is Kontron Product Manager at next system
www.nextsystem.at
www.ctr.at
www.kontron.com
Kontron Modular Computers GmbH
Sudetenstraße 7
87600 Kaufbeuren, Germany
Tel: +49 8341/803-428