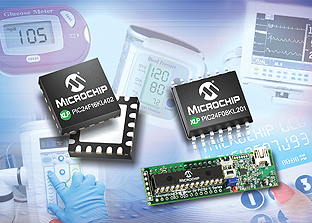
Endoscopes, staplers and hair-removal lasers are amongst the medical products which have
disposable accessories. Rather than being sterilised and reused, these are designed to be discarded after a procedure.
by Jonathan Dillon, Microchip Technology Inc.
Supplied in sterile, sealed packaging, these single-use accessories will only be opened before a procedure. Being disposable, they can be lower cost, lighter weight and more flexible, since they do not have to withstand the sterilisation process or be robust enough for repeated use. There are concerns from manufacturers regarding related to third parties refurbishing and
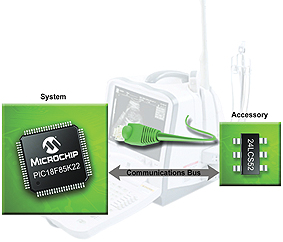
re-sterilising the unit for re-use, exceeding the unit’s design life and possibly compromising hygiene. Together with these primary concerns, other dangers include an incorrect accessory being used, or the accidental use of an expired unit.
If digital control or measurement is already a part of the system, then it is possible to add an electronic communications link to the disposable portion. Figure 1 shows the simple configuration required for the system to identify the individual accessory, retrieve additional data and record usage data in an integrated memory device embedded within the disposable accessory.
There are a number of different types of data held within a disposable accessory that a medical device manufacturer may want to retrieve.
Usage Statistics
Even disposable accessories can record that the unit has already been used and note the serial number of the equipment involved. Recording this information in the accessory itself guards against improper reuse with another system, even if this data can also be recorded by the equipment. Such devices can also measure the total duration of use or numbers of usages, for accessories with specific lifespans.
Calibration Information
All accessories produced should be identical but the effect of manufacturing tolerances, processes and chemistries may cause significant variation between units or batches. The system may be able to compensate for these variations, if they can be highlighted at the production stage. Accessories can be tested at the manufacturing stage to determine their performance, and their compensation values can be stored in the memory.
Storing this data in the accessory makes the compensation seamless to operators, and ensures that the accessory and its calibration data are not separated or mixed up.
Expiry Date
To program the medical accessory with an expiration date only requires that the system console has the current date and time, to compare against the accessory’s expiry date. Once this is established it is easy to verify whether it has exceeded its shelf life.
Model No
The accessory’s model number can be used to ensure it is the correct accessory for the system, and to indicate the accessory type for systems that accommodate multiple disposable -attachment categories.
Serial No
Health-care management may require that the system records the serial numbers of every attachment used, for the collection of warranty information and the statistical analysis of failures. If the manufacturer has communication link to the equipment in the field, recall management could be automated with an instruction to equipment to reject specific serial numbers.
Implementation
An interface to the accessory is all that needs to be added if the system already uses a microprocessor or microcontroller. A serial protocol is well suited for the limited volumes of data that need to be transferred then only an interface to the accessory needs to be added, if electrical contact can be made between the accessory and the system. This also fulfills the low-cost and small-physical-size requirements of disposable medical accessories. If the system has an internal serial bus, then this can be extended to the accessory.
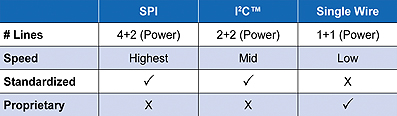
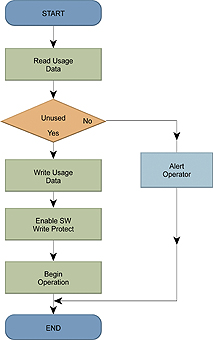
A serial memory device can be used to minimize complexity and components, since the electronics in the accessory need only communicate and store data. Serial memories are available with a variety of communication busses; Table 1 lists the advantages and disadvantages of various options.
Rapid communications are delivered by SPI but the 6 lines and power lines require physically larger and more expensive connectors between the system and the accessory.
I2C™ protocol and single-wire busses, such as Microchip’s UNI/O® protocol are much better suited to these applications. Slower communication speed ceases to be an issue given the limited volumes of data required by disposable medical accessory applications. The reduced number of electrical lines required by these protocols allows smaller, lower-cost connectors and potentially more reliable communications. The two-wire I2C communication protocol is simple to implement and also has the advantage of being synchronous, so it doesn’t have tight timing requirements.
Many microprocessors and microcontrollers support I2C via dedicated on-chip hardware to manage the bus, in contrast to single-line communications protocols which often require software to manage the bus—though this software is widely available—or the use of a translation bridge device. There are several competing, proprietary single-line protocols. The leading single-wire protocols support self clocking or clock recovery, which removes the requirement of high-precision oscillators on both ends. Low data rates allow the use of long, highly capacitive cables and simple signal noise filtering. Power can be supplied over the data line with many single-wire communications protocols, which eliminates the supply-voltage connection, but some external components may be required.
Memory Device Selection
Numerous suppliers offer I2C or single wire interfaces for low-cost serial Electrically Erasable Programmable Read-Only Memory (EEPROM) devices. Storage capacity can range from 128 to over one million bits, enabling the memory to be matched to the specific needs of the application. Small device packages, such as the SOT-23, SC-70, and bumped-die Chip Scale package types, allow for easy integration into the disposable accessory without significantly altering its size and shape. EEPROM technology also offers highly robust storage for more than 200 years at high temperatures.
The system can re-write the data stored in the accessory whilst it is in use, allowing the usage information to be updated and the system to indicate that the device should be discarded.
Alternatively, the accessory’s data can be re-written to record its usage history, as shown in Figure 2. Writes to the EEPROM are performed quickly, but it is a good practice to read from the memory afterward to verify that the write occurred and was completed, since the accessory can be disconnected at any time. EEPROM offers high endurance, allowing each memory bit to be rewritten more than 1,000,000 times, allowing usage data to be frequently updated without “wearing out” the memory.
Serial Presence Detect (SPD) EEPROMs support software write protection provides additional security because a command is required in order to lock and unlock a portion of the memory for writing. This protects against erroneous writes by the system, caused by deviations from normal operating conditions. A further subset of EEPROM devices has permanent write-protection schemes which, once enabled, cannot be unlocked. This could be used to indicate that an accessory has already been used, by writing usage information to the memory before enabling the protection. The protection scheme prevents the information from being reset by third-party refurbishers but allows usage information to still be read by the system. SPD devices are I2C based and are produced by all of the leading EEPROM manufacturers. These devices are also standardised, which avoids single-sourcing issues. There are SPI EEPROM devices with additional options for write protecting certain portions of memory for sophisticated systems that can tolerate the increased number of connections.
Programming embedded memory during the manufacture of disposable accessories gives manufacturers the ability to program model numbers/types, serial numbers, batch calibration, expiration dates or the maximum number of allowed uses into each device so they can be tracked and used appropriately throughout its lifecycle.
www.microchip.com
Note: UNI/O is a registered trademark of Microchip Technology Inc. in the USA and other countries. All other trademarks mentioned herein are the property of their respective companies.