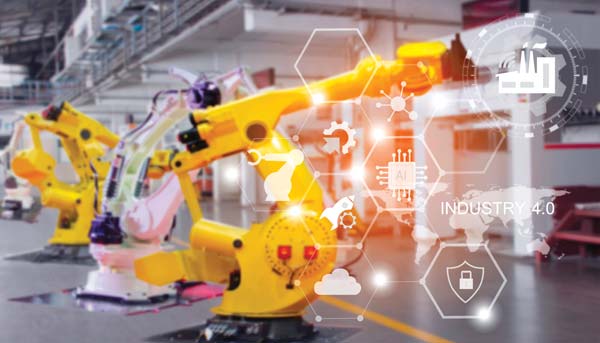
Smart factory automation is already well established in many industries, but with the progress in Artificial Intelligence (AI), remote communication and the growing demand for shorter customer lead times, it is predicted to explode in coming years. — (Image source: Shutterstock / PaO Studio / PRBX)
With a lot of uncertainty in the global economy, trade wars, BREXIT, a lack of qualified operators, 99.99% quality requirements and many others, the transformation of the industrial landscape from conventional to smart is accelerating. In a study published by the Capgemini Digital Transformation Institute, they estimate that within the next five years smart factories could add as much as 1.5 trillion USD to the overall industry. This is really significant and if only a portion of that amount is represented by power supplies it is not a negligible growth.
However, that will require a lot of technical innovation from power supplies manufacturers to meet customers’ expectations.
At a time when some are talking about Industry 5.0 that will focus on the co-operation between man and machine, Industry 4.0 is still at an early stage, though the growing numbers of applications is truly impressive. A lot has been written about Industry 4.0 and intelligent power solutions but since 2015 we have seen other segments such as medical moving forwards to smarter levels of automation and a growing number of robotics requiring power supplies meeting both industrial and medical safety approvals.
Small and medium size robotic equipment is becoming more common place across all industries and if we are used to the impressive robots operating in the car or heavy industries, there is a myriad of smaller robots accomplishing complex tasks, assisting people to improve life (e.g. home healthcare robotics helping disabled people in daily tasks) and even helping surgeons in complex operations, some even being performed by remote control miles away from the surgery theater. The surgical robotic segment alone is expected to grow from USD 3.9 billion in 2018 to USD 6.5 billion by 2023, which is only a fraction of the 600,000 robotic units projected in 2023.
Smart power to small and medium robots
Powerbox (PRBX) and its parent company COSEL are developing power solutions for demanding industries and in both industrial and medical segments we see a strong demand from systems designers for a new generation of power supplies with lots of built-in functionalities, requests for higher flexibility levels in configuration, and more communication interfaces.
The industrial and medical segments are influenced, at one point or another, by the Internet of Things (IoT), and for connected devices from a few watts to multi-kilowatts, communication is becoming very important. We are used to CAN Bus or PMBus but in the smart industry, power supplies will become an active part of the machine-to-machine architecture embedding radio communication and using much faster Bus communication that what is currently in practice.
For many it might seem like science fiction but already today, power systems used within the car industry are able to control and test Lithium-ion battery charging during the car assembly process, operating as an autonomous equipment transferring charging information data to the next work station to continue charging and testing without disruption. All power supplies are communicating via radio transmission, making it possible for car manufacturers to physically move charging equipment to accommodate ever changing production needs.
Another interesting area is the new generation of small and medium size robots deployed in various industries and the medical sector. The level of integration is impressive, requiring power supplies manufacturers to integrate more features such as IGBT gate drivers with high isolation in addition to normal power channels, without mentioning the flexibility required by designers in terms of output voltage combinations (figure 1).
Adding challenges to challenges
Because small and medium size robots are used differently in various industries, robotics equipment manufacturers often require power supplies to comply/certify with industrial standards such as EN62477-1 (OVC III) making it possible to connect the equipment directly to the distribution panel, but also with the new EN62368-1 which was originally created for audio, video and ICT equipment, without forgetting medical standards such as IEC 60601-1 and collateral.
Additionally, power designers have to consider a large raft of safety and operational standards, adding yet another level of complexity to an already challenging environment.
Smart industry also means a smart way of organizing factories, with site developers optimizing factory and workshop layouts to increase flexibility and efficiency. Examples include minimizing the main power cabling to equipment, and exchanging Ethernet and other data transmission cabling for ruggedized and secure RF communications.
Industrial RF communications networks will develop to facilitate machine-to-machine communications and although power supplies might not need built-in RF transmission capability, they will need a higher level of interaction with their surroundings compared to now, and as it has been in the car industry, it could become a must for certain applications.
RF communication is an interesting research area for power designers to explore, and similarly, how power supplies will follow the machine-to-machine evolution.
Smart power to smart factory automation
Smart factory automation is already well established in many industries, but with the progress in Artificial Intelligence (AI), remote communication and the growing demand for shorter customer lead times, it is predicted to explode in coming years. Similarly, the growth of automated parcel-hubs is expected to rise spectacularly. The rapid development of e-commerce has contributed to the creation of highly automated hubs with conveyers, sorting switches and many other equipment requiring efficient and intelligent power solutions able to work in demanding environments.
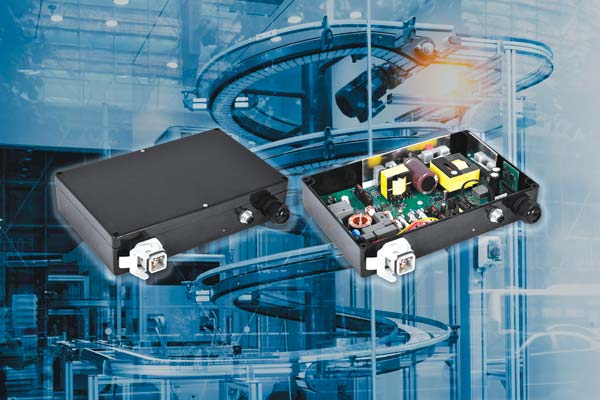
Figure 2: PRBX ENI250A24 designed for high speed e-commerce hubs conveyers with microprocessor controller and energy recycling.
Parcel hub-designers and hub-operators are facing multiple challenges in having to deal with a large variety and types of equipment. The new generation of parcel hubs are built on a very sophisticated architecture. Instead of having (say) a 100-meter long conveyer belt, the new lines are composed of shorter individual segments five to ten meters long, and turned on and off on demand when a parcel is transported from point A to point B. Each segment is powered by a DC motor requiring the use of an advanced power supply able to not only deliver power but also to meet the complex requirements inherent to the modern parcel hub environment.
Traditionally, below 1000W, DC motors are powered by a single-phase AC/DC power supply.
Though to simplify installation, reduce unbalanced phase loading and for better optimization of energy from the grid, parcel hub designers now require that all power supplies for DC motors have a three-phase input, and for whatever the power level. Also, considering energy saving and reducing peak-loads, hub designers require power supplies to include peak energy control and energy storage, thus able to store energy when motors are decelerating or stopping, but also to deliver high energy levels when DC motors are activated. This is usually achieved by capacitors or supercapacitor banks partly controlled by the microprocessor in charge of the power supply energy management (Figure 2).
The smart power revolution is coming
Those two examples illustrate the changes in demand from systems designers, the levels of innovation required, and the challenges that power supplies manufacturers will face. This is a really exciting time for power designers, not just to think out of the box, but to add more to the box.
Author: Patrick Le Fèvre, Chief Marketing and Communications Officer
Powerbox – A Cosel Group Company| www.prbx.com
References:
POWERBOX (PRBX): https://www.prbx.com
COSEL: https://en.cosel.co.jp
Capgemini: “How can manufacturers realize the potential of digital industrial revolution” https://www.capgemini.com/gb-en/resources/smart-factories-how-can-manufacturers-realise-the-potential-of-digital-industrial/
Editor note:
Article reproduced with courtesy of Power Electronics News and Powerbox (PRBX) – URL: Power Electronics News https://www.powerelectronicsnews.com