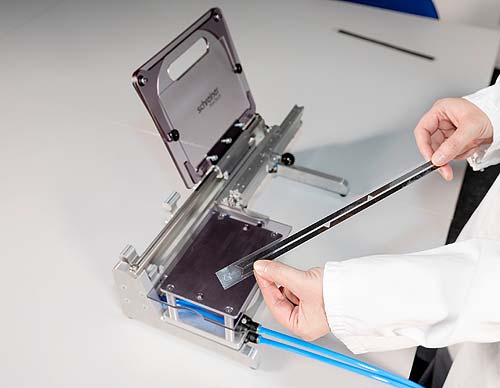
Picture of the Folding Frame System: The specially developed system picks up the strips, folds them apart and joins the components with each other. The possibility of semi- or automatic processing ensures exact repeatability and thus reproducibility.
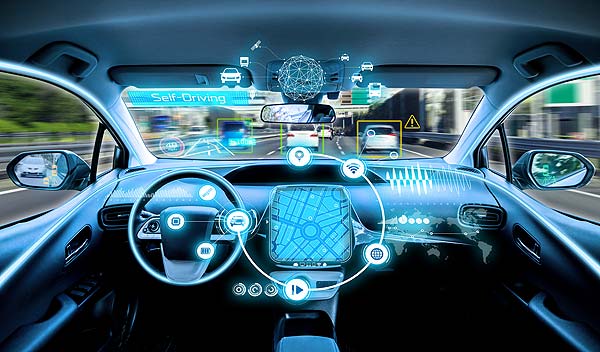
Schreiner ProTech offers solutions for component connections, e.g. for displays in the automotive industry.
Possible Methods of Bonding Components
Bonding of diverse components requires utmost precision to ensure that the parts are accurately and neatly placed on top of each other in order to guarantee perfect functionality of the final product. Adhesive frames created from full-surface cutouts are commonly used for this purpose, but produce a lot of waste. The material is typically available only in the form of single units or sheets. Due to this form of delivery and the frame dimensions, automated solutions are expensive while in manual processing, the risk of faulty adhesive bonding cannot be excluded. By contrast, the utilization of adhesive tape saves material, but in manual processing leads to small gaps or overlaps in corners. As a result, the component connections are neither watertight nor dustproof. Liquid gluing is another method that can be used to connect complex geometries. However, the curing times of liquid adhesives slow down the assembly process and their flow behavior usually prevents accurate and clean adhesive bonding.
Due to the production of a foldable adhesive version instead of a frame created from a full-surface cutout, multiples can be achieved more efficiently and material consumption significantly reduced for sustainable and eco-conscious manufacturing. Self-adhesive bonding solutions support the lightweight design megatrend and replace bolted, riveted and soldered solutions. In addition to bonding and sealing, foam-based adhesive tapes make it possible to equalize uneven areas or height differences and reduce noise.
Schreiner ProTech together with the Schreiner Services Competence Center offers customized system solutions. The product solution and matching processing system are supplied by a one-stop shop.