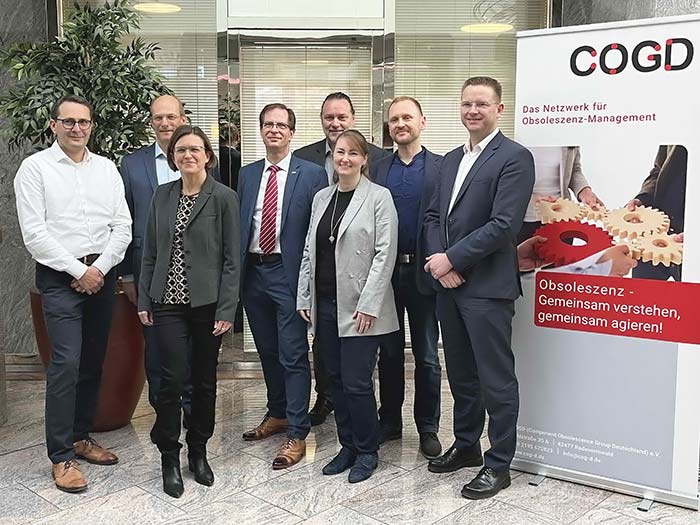
The current board members are delighted with what COGD has achieved in its 20 years: (from left): Sven Sander (Schaeffler Automotive Buehl), Deputy Chairman Martin Steinleitner (Syliom), Janine Keller (OneSubsea), Chairman Axel Wagner (Asteelflash), Dieter Paatsch (Festo), Stefanie Kölbl (TQ Group), Frank Mützner (Plastic Omnium Lighting Systems), and Oliver Hoffmann (Z2Data).
The non-profit industry organization COGD (Component Obsolescence Group Deutschland) e.V. recently celebrated its 20th anniversary. Together with its association members, COGD has set itself the goal of identifying and analyzing obsolescence risks for manufacturers of durable goods at an early stage and developing strategies to prevent obsolescence or at least minimize its negative consequences.
In safety-critical areas and industries such as military technology, aerospace, and rail, where systems usually have to remain in service for many decades, ensuring long-term system availability has been a major challenge for many years. NATO programs such as DMSMS (Diminishing Manufacturing Sources and Material Shortages) also pointed out early on the need for comprehensive obsolescence management in the military and public sectors. But it was not until 1997 that the first Component Obsolescence Group was founded in the UK on the initiative of two Bombardier employees, Detlef Blum and Richard Russel.
Obsolescence strategies
The idea of working together with component manufacturers, service providers, and other manufacturing companies threatened by obsolescence to find solutions for eliminating or reducing obsolescence risks proved so successful in practice that eight years later, a similar organization was established in Germany, initially as a subgroup of COG UK. Launched in spring 2005 under the chairmanship of Mike Bews from the UK with 30 industrial, commercial, and service companies mainly from the electronics industry, the COGD has grown over the past two decades to become the most important national dialogue platform for active and strategic obsolescence management and the largest national chapter of the International Institute of Obsolescence Management (IIOM), the successor organization to COD UK.
Comments
Axel Wagner, honorary chairman of the COGD and full-time corporate lawyer for the EMEA region at Asteelflash Holding, pointed out to the guests and association members attending the COGD’s 20th anniversary event that this positive development was being viewed with mixed feelings. “Of course, we are delighted about the continuous growth in COGD membership, but the sharp rise in membership is unfortunately also proof that materials, software, electronic components, and other replacement parts that have been discontinued or are suddenly no longer available on the free market for other reasons have become a serious problem for more and more industrial companies in recent years,” said Wagner.
The main victims are still equipment and plant manufacturers in sectors such as automation, automotive, rail, medical, military, and production technology, which sometimes have to provide spare parts for maintenance for decades, while the product life cycles of the parts, components, and software programs used are becoming shorter and shorter and other obsolescence risks such as geopolitical upheavals, natural disasters, stricter environmental regulations, and cyberattacks are also increasing. “Product discontinuations have always existed. However, their number has exploded in the last two decades, especially for electronic components. One of the reasons for this are the extremely short life cycles of smartphones, smart watches, and other innovation drivers in the consumer sector. But in other areas that are important for security of supply, such as the resilience of international supply chains, the cost of taking precautions has also risen significantly. Keeping an eye on all latent risks in the supply chain and acting accordingly in a forward-looking manner is therefore often a major personnel and financial challenge, especially for medium-sized companies,” says Wagner, speaking from many years of experience.
The best possible advice and support
Like his predecessors Dr. Wolfgang Heinbach, Ulrich Ermel, and Detlef Blummit, Axel Wagner and his COGD board colleagues have set themselves the goal of providing affected companies with the best possible advice and support in overcoming these increased challenges. This includes not only specialist presentations by renowned experts at regular quarterly meetings, various internal working groups on a wide range of topics, dialogue platforms for direct personal exchange between members, in-house exhibitions, and public lecture series organized by the COGD at trade fairs and international conferences. During the ceremony, the chairman of the board of the multi-faceted industry association also referred to other successful COGD initiatives, such as the inclusion of the smartPCN standard initiated by the COGD in the IEC 62402 standard, the cooperation with the law firm ReachLaw, and the involvement in the electronics association alliance, in which the COGD, together with the FED (Fachverband Elektronikdesign und -fertigung e. V.) and the FBDi (Fachverband der Bauelemente Distribution), is calling for extensive bureaucracy reduction in the electronics industry. “The continuous intensive exchange of information and data with manufacturers, associations, political organizations, and other association members will remain crucial for eliminating or at least reducing obsolescence risks in the future. Efficient obsolescence management requires companies to address potential weaknesses in the supply chain as early as possible, i.e., not just shortly before the start of series production, but already during the evaluation and development phase of a new product. However, an early comprehensive risk analysis requires a correspondingly large, constantly updated, and, if possible, automatically processable database. And, of course, the necessary expertise and extensive experience. Interested companies and individuals can gain plenty of the aforementioned at COGD, and we will do everything we can to ensure that this remains the case for the next decades”, says Axel Wagner.
Interested parties can find detailed information about the activities of Component Obsolescence Group Deutschland e.V. on the association’s website at www.cog-d.de.
COGD (Component Obsolescence Group Germany) e.V.