
Developers of mobile applications, as well as gaming and automotive applications were the first to know the options for utilizing the MEMS sensors.
The sensors also open an abundance of options for application in industry, medicine and home appliances sphere.
Especially attractive for many applications are the 3-axis acceleration sensors. With costs of significantly less than one Euro and a multitude of features, they provide a first class price/performance ratio. Included in the actual highlight products are the 3-axis MEMS acceleration sensors LIS3DH from STMicroelectronics and BMA250E from Bosch Sensortec.
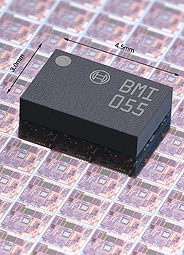
Both are extremely low consumption and small and, therefore, are also recommended for applications mobile appliances. Due to Low Power mode, the power consumption of the ST model LIS3DH can be reduced to only 2μA, the sensor from Bosch requires less than 5μA. With the aid of their “Wake-up on Motion Function”, the power consumption for a complete application can be significantly reduced and the service life of the battery increased. The application is set to a form of “Sleep mode”, when the MEMS sensor registers motion it is “awakened” (Smart Power Management). The dimensions of 3×3×1mm (LIS3DH) and 2×2×0.95mm (BMA250E) of the sensor housing are ideal for applications where space is critical. Both models provide accurate values across programmable measurement ranges of ±2g, ±4g, ±8g and ±16g with a sensitivity of 1mg/digit for the LIS3DH and 256LSB/g for the BMA250E in the 2g range. They have a digital resolution of 12 Bit and 10 Bit, the typical zero-g offset over the complete service life is ±40mg for the ST and ±80mg for the Bosch model.
Many features open countless options for application
Both acceleration sensors provide “Freefall Detection”, which at present is primarily utilized in hard drives of laptops. Here, the write and read head is placed in a safe position as soon as the sensor registers the freefall. This principle can also place machines, e.g. chain saws or remote crane control, in a safe condition by freefall using emergency shutdown.
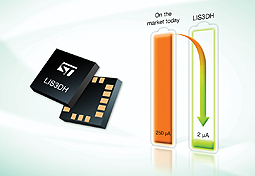
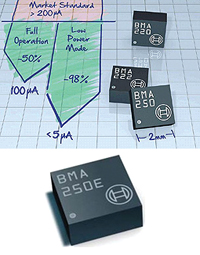
Due to the recording of the most minimum of motion and vibrations, as well as changes in position, the acceleration sensors are also suitable for protection against vandalism or theft, for example for oil or gas pipelines, machines or valuable objects. Registration of vibrations can serve to check the correct function of a machine and, in the event of a malfunction, quick shutdown.
HMI applications can be provided utilizing the sensors with new features and, thus, enhanced. With the aid of the so-called “display profile switching”, alignment of the screen can be adapted to portable control units with displays if the display is rotated through 90° – similar to digital cameras.
Their Flat Detection allows by detection of the position for example disabling the sound (Smartphone) or the shutdown of an appliance if there are vibrations.
In many applications, the acceleration sensors provide tap and double tap control. Thereby, there is no requirement for mechanical buttons and, thus, easy control is provided.
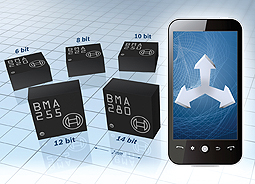
The step counter function is attractive for mobile fitness or health monitoring, as well as the Activity Monitoring that can be realized by the 3-axis acceleration sensors. Motion patterns of the carrier are recorded and, thus, conclusions made of the route covered and the calorie consumption. In the event of a fall, e.g., whilst mountain climbing, the sensor detects the freefall and, if the body no longer moves can initiate an emergency call.
For initial tests using the MEMS sensors, the STMicroelectronics and Bosch Sensortec provide software and hardware tools with a user-friendly graphic user interface. Thus, developers can vividly carry out different adjustments and tests and later transfer this to the application one-to-one. For this, both manufacturers provide programmable boards, Application Programming Interface (API) and Low-Level drivers.
Abundance of sensor types
In addition to the acceleration sensors, there is a wide range of other types of MEMS sensor on the market. Thus, MEMS microphones combine a high quality of sound and robustness with the smallest dimensions for applications of speech recognition and control. In contrast to conventional classic electric microphones (ECM), the MEMS models are more reliable and robust and have better characteristics over the temperature curve. At present, they are hardly more expensive than the conventional microphones; shortly they will be available for the same price or less.
They are not only suitable for HMI applications in industry, but also for navigation systems, hands-free systems or conference systems. STMicroelectronics offers digital (MP34DT/DB01 / MP45DT02) and analogue (MP33AB01/B01H) models with a SNR of up to 63dB at a very flat frequency response (20Hz to 20kHz).
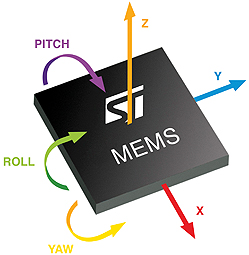
For example, gyroscopes contribute to more safety in drills.
They record the rotation of the drill (or concurrent rotation) after the drill has engaged in the concrete and provides emergency shutdown. Barometric MEMS pressure sensors measure the air pressure and, from the value, calculates the height to within an accuracy of 25cm. Thus the pressure sensors open up new application scenarios for indoor navigation in stores or car parks. This could even assist the fire service and police to save life, whereby they indicate the location of persons who have had an accident. In navigation systems, they depict the exact position of the vehicle, also on multi-level roads.
With the combination of multiple sensors, the options expand practically indefinitely.
For example, in a washing machine: here, the pressure sensors could measure the fill level whilst the acceleration sensors determine the load and optical sensors check the degree of contamination of the water, so that the wash/drying program can be optimally adapted.
Sensor combinations
The manufacturers have also recognized the advantages of combining different types of sensor and already provide these united in a module, e.g. in the LSM330D from STMicroelectronics.


The 3-axis acceleration sensor LIS3DH and the 3-axis gyroscope L3GD20 are located in a housing only 3×5.5×1mm in size. The latter provides the full measurement scale from ±250dps to ±2000dps and has a programmable interrupt. The same combination of 3-axis acceleration sensor (BMA255) and 3-axis gyroscope (BMG160) is provided by Bosch Sensortec, with the BMI055. With the dimensions of 3×4.5×0.95mm, it is the smallest Inertial Measurement Unit (IMU) available on the market at present. Its six (6DoF, Degrees of Freedom) and low power consumption of only 5.15mA in full operation mode makes it ideal for demanding applications in the consumer electronics, e.g. for gaming applications for play consoles, Smartphones and tablet PCs. Its high resolution of 16 Bit (gyroscope) and 12 Bit (acceleration sensor) provides accurate, reliable measurement results. In addition, the BMI055 has an excellent signal/noise ratio. Its measurement scale enables it to be programmed, from ±125dps to ±2000dps for the gyroscope and ±2g to ±16g for the acceleration sensor. Moreover, the latter distinguishes itself by a low Zero-g-Offset of typically only 70 mg. The digital I2C and SPI interfaces provide flexible options for data communication.
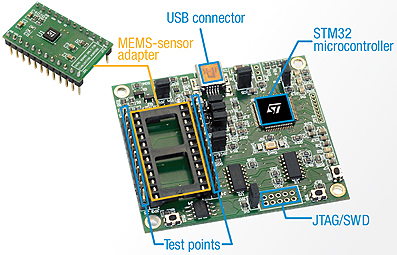
The types of xDoF MEMS sensors and modules not only enable gaming applications, but also remote monitoring of patients or older people without restricting their freedom of movement. Thus, the sensor can, e.g. “detect” a fall and initiate an alarm to the careers. Also mentally confused persons who have strayed can be found. Ergotherapy, training for sports persons and medication information can be accurately determined for the individual movement profile and, thus, can be applied more effectively. The sensor can check the position of the arm in blood measurement appliances at home and, thus, ensure correct measurement. In livestock breeding, with the aid of such a MEMS sensor, the quantity of concentrate can be individually determined to the movement of the animal.
All in one
Sensor modules that combine a greater number of sensor types have even more freedom of movement.
STMicroelectronics has recently introduced such a Multi-Sensor module to the market with new degrees of freedom: the iNEMO M1 (System on Board) unites a 6-axis
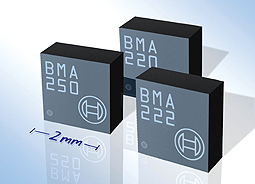
geomagnetic sensor LSM 303DLHC (3-axis acceleration sensor + 3-axis magnetic sensor), a 3-axis gyroscope L3GD20, as well as the 32-Bit micro-controller STM32 and a specific Sensor Fusion Software – and that with dimensions of just 13×13×2mm. Thus, the iNEMO M1 has nearly all perceptions of the human sense and that partly exceed this. Thus, it records linear accelerations, angular speeds and the earth’s magnetic field, with which the position, movements and their directions can be accurately determined. The software gathers the output signals of all sensors. Contortions and inaccuracies of the measurements are automatically corrected by prediction and filter algorithms. The gyroscope L3GD20 registers roll, pitching and pivoting movements on an arbitrarily selectable scale of between ±250°/s, ±500°/s and ±2000°/s. The geomagnetic sensor LSM303DLHC has an arbitrarily programmable measurement scale of ±2g, ±4g, ±8g and ±16g for the acceleration sensor and ±1.3 Gauss to ±8.1 Gauss for the magnetic sensor, as well as an I2C output. With these features, the iNEMO introduces more

reality into gaming and virtual and augmented reality applications, human-machine interfaces, robots and portable navigation appliances, as well as for monitoring patients.
Development support
The abundance of different types of MEMS sensors with different levels of integration spoils the developer for choice. Frequently it is initially difficult to say with which type of sensor the objective of a development can be best attained. Rutronik has an incomparably wide and broad portfolio of the most different, innovative types of MEMS sensors of its franchise manufacturer. Thereby, the distributor not only covers the sensors, but also the sensor signal processing. From this wide range, a suitable solution can be realized for every requirement and the developer must not already determine at the beginning of the development. They obtain knowledgeable support from the Rutronik product and application engineers. For an overview of the portfolio, refer to the Website www.rutronik.com/sensors.
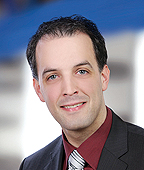
Author: Martin Grimmer, Senior Marketing Manager Analog & Sensors at Rutronik Elektronische Bauelemente GmbH
www.rutronik.com