With the growing concern for the environment and reducing energy consumption, the need to meet governmental regulations, and of course individual initiatives, the demand on power designers to develop very efficient power solutions has been great. But simultaneously and creating even more difficulties, emerging applications have required smaller power supplies with unprecedented power density expectations.
The laws of physics are the laws of physics, and despite many evolutions in switching topologies, power designers have run into road blocks requiring a solution that is able to switch faster, with less power losses and if possible, maintaining good performances at higher temperatures.
Despite technological advancements in conventional semiconductors, it became difficult to increase the switching frequency by a magnitude of 10 while reducing the physical size of the power supplies while also reducing power losses. Among the different routes taken to achieving this, the exploration of materials offering higher performance such as higher-energy electronic band gaps has revealed the potential of Gallium Nitride and Silicon Carbide. Both materials have been used before e.g. SiC diodes and GaN LEDs, but the use of Wide Bandgap FET appeared relatively recently in the power electronics history.
As for all new technologies, GaN FET and SiC FET went through the classic process starting with the Innovators, to the early adopters and now reaching the early majority. What is very interesting is that probably due to a large number of innovators, GaN and SiC manufacturing was very quick off the mark in addressing niches markets with a very high growth potential.
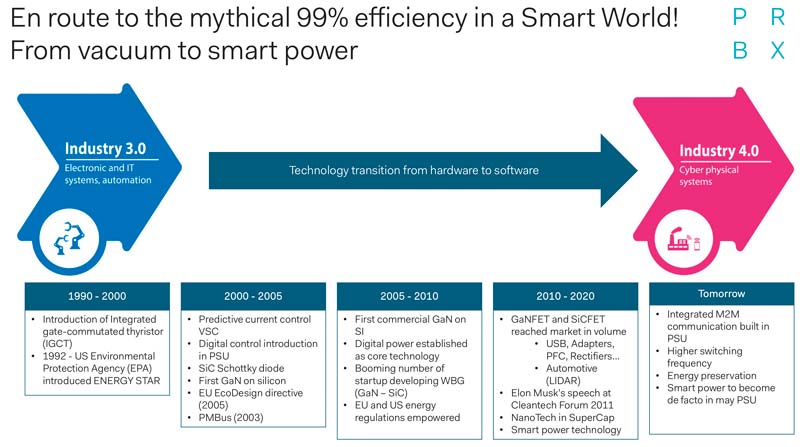
Figure 2: Energy regulations, digital power, wide bandgap semiconductors contributing to lower the energy consumption and to increase energy efficiency.
Wide Bandgap (WBG) technologies have been presented at many conferences but I consider the real kick-off to have taken place in 2018 when “challengers” demonstrated the commercial potential of WBG technology. It is impossible to name all of them but among the leaders promoting GaN, I would say that the Efficient Power Conversion (EPC) Idea to implement GaN in LIDAR (Light Detection and Ranging) (picture 03) was really interesting, especially with that technology becoming preponderant in the new generation of vehicles. 2018 was also the year in which USB adapter manufacturers started to consider implementing WBG. Navitas is another example of an innovative company, which in the early days pushed GaN integration to a higher level by packaging drivers and switches on same substrate. If today, intelligent GaNFET is becoming a standard, it was not the case when Navitas introduced that concept.
If WBG is a very promising technology, we should keep in mind another symbolic milestone for a technology called ‘Digital Power’ that emerged in 2003 as a promising technology. As it was for digital power 17 years ago, GaN, having started its journey only a few years ago has followed a similar path, gradually migrating from a ‘technical curiosity’ to a ‘commercial product’. Digital power and GaN are both technologies that were challenged and highly debated when introduced to the market, and it is interesting to link both of them in this way, especially when the outcome of combining the best of the two technologies results in truly outstanding commercial products.
Step by step to maturity
As it is for any new technology – especially when disruptive – the transition from research level to high volume production is a long process, one that includes new learning for electronics engineers and in the case of GaN, the implementation of zero-voltage switching topologies requiring very specific drivers and new ways of controlling them. Despite the huge benefits of GaN transistors, for many years the lack of drivers limited the interest level from industrial designers. Thankfully, the increased number of semiconductors players investing in GaN in the last two years has made this technology simpler to implement.
Many technical barriers have been removed. Manufacturing processes have gradually been optimized to increase yield and reduce cost, quality processes specific to this technology have been implemented, and in November 2017 the JEDEC organization announced the formation of a new committee to set standards for Wide Bandgap Power Semiconductors (JC-70). Following on, February 2019 saw the release of the publication JEP173: Dynamic On-Resistance Test Method Guidelines for GaN HEMT Based Power Conversion Devices. Step by step, the puzzle is being solved and if GaN has been widely used in LED and RF applications for many years, power supply manufacturers for commercial products deployment are now adopting it.
Digital power combined with GaN heads towards 99% efficiency
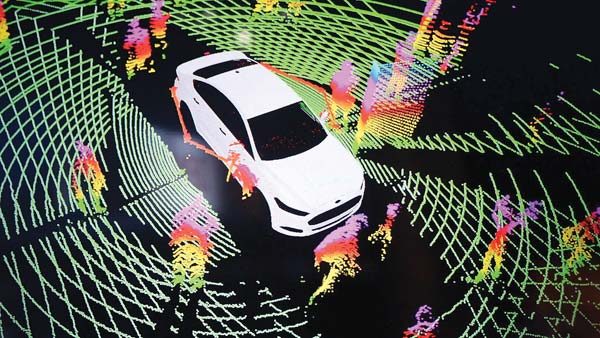
Figure 3: GaN in LIDAR (Light Detection and Ranging) very promising and foreseen as high volume application for GaN power semiconductors
What makes power designers’ lives so exciting is the ever-present levels of innovation making it possible to improve performance levels, thus contributing to reducing our environmental impact and the creation of a sustainable society. Combining the benefits of digital power with GaN performance and the ability to switch at high frequencies with low power losses makes it possible for designers to develop very high-power density units. That combination results in smaller products with lower power dissipation that are ready for stringent, future regulations foreseen in the coming years (e.g. micro-amps for standby power). One practical example is USB chargers where by combining digital and GaN, several companies are in some cases almost tripling the power density for a standard USB charger. That is without talking about multi kilowatts power factor correction equipment fitting into an existing 500W footprint. We are all aiming to break limits and there is no doubt we are moving fast towards the 99% efficiency, but as power designers we have to consider a new dimension that includes a larger eco-system.
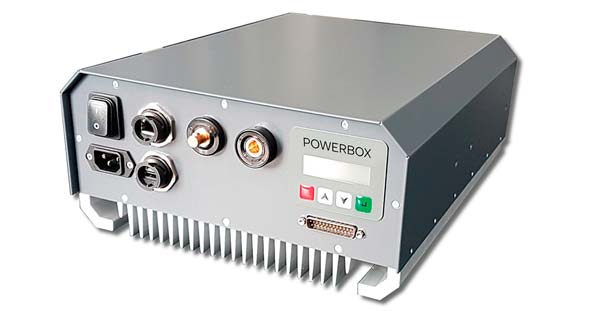
Figure 4: PRBX intelligent battery charger with radio communication interfacing with the factory Hub Process Controller (HPC). The unit communicates with its ecosystem and information exchanged with other power units to optimize e.g. charging profiles. Smart power supplies include very advanced energy management controller, optimizing performances to loads and environment.
Smart power becoming a reality
WBG and digital power have brought strategic, exiting technologies to the power designers’ toolbox, and every day we are achieving new limits, but in today’s world and as an effect of the industry’s transformation, power supplies have to be both energy efficient and perform equally well within the eco-system in which they are integrated. From a USB-PD +PPS for charging and communicating with a battery, to a huge factory automation system where all power supplies are dynamically controlled and optimized to reduce factory energy consumption, power supplies designers will have to include a new dimension when designing the next generation of power solutions.
If previously, the well-known PMBus communication between a power supply and a power/site manager was well understood, then including Machine-to-Machine (M2M) communication with direct control of the power supply is relatively new and only at the beginning of its journey.
Industry 4.0 will introduce a higher level of software integration and if many power supplies remain as standalone units, we foresee a significant number of applications requiring power supplies to interoperate within their eco-system in a very advanced way (picture 04). Smart Power for a Smart Industry is becoming a reality, and a very exciting one at that.
In conclusion
Smart Factories will use Smart Power solutions designed by Smart Power Designers all aiming for 99% efficiency, but with another eye on the ambitious target of 99.99%!
Author: Patrick Le Fèvre, Powerbox Chief Marketing & Communication Officer, Powerbox
About the author:
Chief Marketing and Communications Officer for Powerbox, Patrick Le Fèvre is an experienced, senior marketer and degree-qualified engineer with a 35-year track record of success in power electronics. He has pioneered the marketing of new technologies such as digital power and technical initiatives to reduce energy consumption. Le Fèvre has written and presented numerous white papers and articles at the world’s leading international power electronics conferences. These have been published over 250 times in media throughout the world. He is also involved in several environmental forums, sharing his expertise and knowledge of clean energy.
Powerbox – A Cosel Group Company| www.prbx.com
Powerbox – A Cosel Group Company
Editor’s Note: Article reproduced with courtesy of Power Electronics News and Powerbox (PRBX)
URL to PEN and PRBX to be embedded: PRBX: https://www.prbx.com/
Power Electronics News: https://www.powerelectronicsnews.com/