Würth Elektronik has developed a new testing procedure for determining the maximum operating voltage of molded inductors. The manufacturer of electronic and electromechanical components introduces developers to the electrical property of dielectric strength and what happens if it is exceeded in an application which is described in Application Note 126 (www.we-online.com/ANP126). The molded inductors from the Power Magnetics product portfolio (e. g., WE-MAPI, WE-XHMI, WE-LHMI) are now successively supplemented with the value of the maximum operating voltage Vop as a new parameter in the specifications.
Based on the new testing procedure, Würth Elektronik defines the maximum operating voltage Vop in its data sheets. This represents the voltage at which an inductor can be operated continuously in the application without impairing performance, risking damage or overheating the inductor. The operating voltage is therefore a limit value for the input voltage, up to which the inductor can be used reliably in an application without irreversible damage.
The test concept examines the behavior of inductors up to their voltage limits under realistic conditions in a DC-DC full-bridge converter (voltage transients of up to 60 V/ns and frequencies of up to 2 MHz). The approximate voltage limit is firstly evaluated using a short-term test. The operating voltage is then defined on this basis and verified in a long-term test.
Background
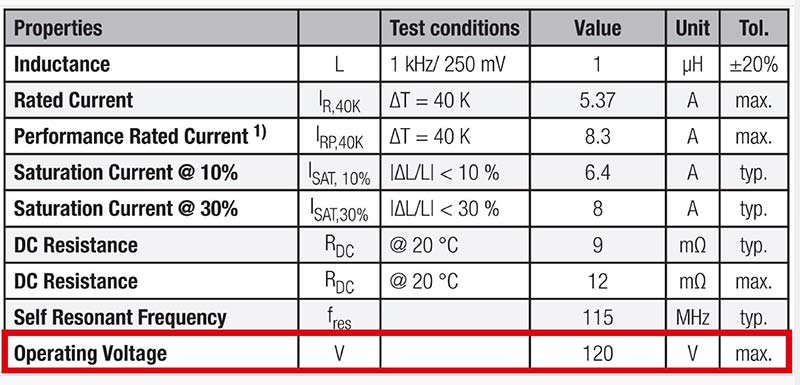
The new product characteristic in the data sheet clearly indicates the maximum operating voltage of the inductor in the application. — Image source: Würth Elektronik
Thanks to steady technological advancement in the semiconductor industry, today’s MOSFETs can now achieve high current densities and short switching times. For this reason, the question of the dielectric strength of coils has become increasingly important in recent years when it comes to selecting the appropriate inductor.
What’s more: Continuous optimization of the production process and the material composition of molded inductors enable high permeability of the ferrite material to achieve the highest possible inductance values in the smallest possible package space. The power density per volume can therefore be raised continuously.
This entailed a steady increase in the proportion of iron powder or iron alloys relative to the insulation of the binder, resulting in the distance between individual grains becoming progressively smaller. If the insulation barrier between the individual metal particles is not high enough for the voltage applied in the application, a conductive path is created through the core material, caused by arcing between the individual metal particles. It may be observed in the application that the profile of the ripple current changes. Schematically, there is now a resistor parallel to the inductor.
The consequences: Self-heating of the coil rises dramatically due to the rising losses. These additional losses considerably reduce the inductor’s efficiency. The advantage of a DC/DC converter – to transmit voltage levels with high efficiency – is lost.