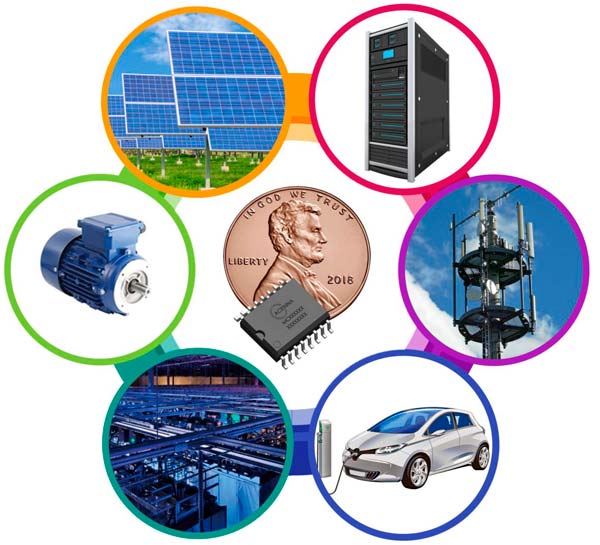
Figure 1: Modern current sensing technologies are available for a wide range of applications – from EV cars and ADAS systems to home appliances, telecommunications and server farms.
The embedded electronics development community is currently experiencing the biggest changes in our industry since the creation of the integrated circuit. From new software-oriented solutions like Artificial Intelligence, to new hardware topologies, to new semiconductor materials, we are in the middle of a disruptive period of demanding growth.
Much of these advances are related to user functionality, like Cloud-based Internet of Things (IoT) solutions that rely on next-generation RF technologies. Other rapidly emerging current sensing applications include Electric Vehicles (EV) and their Advance Driver-Assistance Systems (ADAS) and Autonomous Driving needs, to wide-bandgap power switches based on Silicon Carbide (SiC) and/or Gallium Nitride (GaN) semiconductors. Some of the most important advances in these spaces have been in performance and efficiency, enabling the next generation of electronic solutions to address the challenges and demands of users and the marketplace.
The latest trends in personal electronics put a lot of pressure on the designers of embedded systems. When it comes to consumer and medical wearables, advanced personal electronics, and the internet of things, the smaller, more functional, and longer lasting, the better. Similarly, industrial and automotive applications are pushing boundaries to achieve smaller, more efficient, reliable, and robust solutions. Significant improvement in all of these include reducing parts count, simplifying circuitry, and increasing operational efficiency.
Current-sensing technologies are key to creating the small precision control and protection electronic circuits needed to make the devices of tomorrow serve applications in an efficient and cost-effective manner. There is no precision without feedback, and current sensing can provide the critical performance information an embedded intelligent system needs to manage itself. The size, accuracy and speed of your current-sensing solution will directly impact all of these aspects.
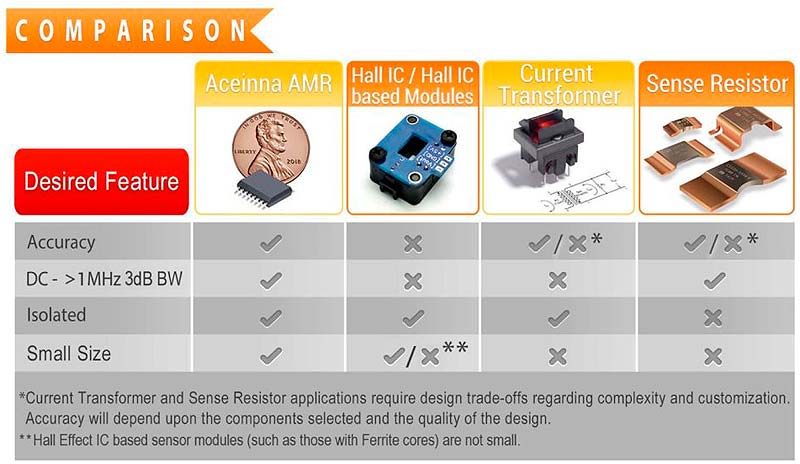
Figure 2: Advantages of AMR based Current Sensing versus other types of current sensing technologies
AMR current sensing
A single-chip solution, the ACEINNA Anisotropic Magnetoresistive (AMR) technology based, isolated current sensor does not require additional components other than a decoupling capacitor. Compared to the other methods of current sensing, an AMR sensor provides a compact and high-performance solution. For example, the problem with using a shunt resistor is that it is inherently not isolated. A current transformer is bulkier than an AMR based current sensor and it only works with AC. Compared to using a Hall-effect sensor, AMR technology offers a bandwidth of 1.5 megahertz, and has a lower offset and noise.
Delivering better performance than a shunt register or transformer, AMR technology can respond to both DC and AC bi-directional current, with a bandwidth of 1.5 megahertz and a lower offset and less noise than Hall-effect-based solutions. Offering better accuracy, higher bandwidth with lower phase shift, and a very fast output step response, an AMR based current sensor is an accurate and compact solution for very critical measurements to protect and control power systems.
Within the sensor, the current flows through a U-bend in the lead frame, where it generates a forward or reverse field measured by two current sensors in the device. By measuring the field from both current directions, the device cancels out the external fields and magnetic anomalies which might be present. This allows a horizontally-sensing AMR chip to ignore external fields generated from other nearby components on the board.
Electric Vehicles
There is a tremendous amount of attention being paid to EVs right now. Much of the focus is on improving the efficiency of the powertrain, motors and On-board/Off-board charging systems as well as the performance of the battery pack, as they are all directly related to vehicle range and charging efficiency. The proper application of current-sensing technology in these application areas can deliver significant advantages.
Since the motors are where the power is being spent, any improvement there will cascade benefits throughout the system, from increasing EV range to reducing thermal management needs. When it comes to driving motors, the switching frequencies and control mechanisms are critical.
Effective motor control requires accurate performance measurement, and for that you need effective current sensors. For condition monitoring of motors for predictive maintenance, fast current sensors help to measure and monitor motor ripple currents to determine lifetime and performance parameters. On the protection side, the current sensor helps support safety by improving the control, accuracy, and reliability of a motor drive.
Many EV power electronics and charging systems are migrating to advanced wide-bandgap semiconductors like Silicon Carbide (SiC) and Gallium Nitride (GaN), as the benefits provided include higher efficiency and the ability to increase the switching frequency. A significant benefit of faster switching is the ability to shrink the size of the passives and magnetics in a circuit, with direct size and weight benefits.
However, when a circuit is switching faster, the ability to measure the performance parameters must be able to keep up, demanding real-time information from a fast and accurate current sensor. Monitoring the circuit in real-time enables advanced functionality like dynamic control of the power switching and motor drive frequency, as well as reliable and fast fault detection.
In the related area of electric trains, industrial machines, traction and robotics, we are starting to see the use of reluctance motors, a winding-free design that generates torque through magnetic reluctance. Available in synchronous, variable, switched and variable-stepping configurations, reluctance motors can deliver high power density at low cost.
The problems with reluctance motors include high torque ripple at low speed, and the resulting noise. In addition, because of the extremely high temperatures involved, reluctance motors are usually deployed with a separate harness and control system. Advanced solutions using wide-bandgap SiC semiconductors and high bandwidth AMR sensors can take more heat, enabling size, weight, and complexity reductions of the overall system, providing cascading benefits.
Constructed without copper coils in the rotor, reluctance motors can be lighter than comparable electric motors. However, the required control system is very complex, because if you don’t accurately control the current, which is related to torque, you’ll get a torque ripple and that generates noise issues. Advanced fast current sensing improves control of the ripple current, which provides lower noise and a more reliable solution.
It’s important to bring up the protection side again because in high-power systems, you might want to switch the whole power stage off in 1.5 microseconds. If you look at that shutdown time budget, your step response needs to be less than 500 nanoseconds, and that’s going to become more stringent as we migrate into higher power and frequency levels.
Power Factor Correction
Used to reduce the lagging power factor in inductive loads, Power Factor Correction (PFC) compensates for the phase difference between voltage and current, for when the power factor drops, the system becomes less efficient. To get 1 kW of real power at a 0.2 power factor, 5 kVA of apparent power needs to be transferred (1 kW ÷ 0.2 = 5 kVA). This obviously can severely impact the performance in the case of inductive loads such as motors, refrigerators and HVAC systems, Inverters, uninterruptible power supplies (UPS), and similar application spaces.
Fast turn-on and -off time, fast reverse recovery and lower ON resistance of wide bandgap SiC and GaN based power switches are allowing effective use of Totem Pole architecture to improve efficiency of PFC and reduce the number of components used. These benefits help power systems to achieve higher efficiency 80+ Gold and Titanium certifications.
For example, when it comes to ripple currents in the PFC in a Totem Pole, to measure current cycle-by-cycle to calculate the pulse-width modulation (PWM) duty ratio, you need to have a high bandwidth for the ability to match the circuit’s switching frequency. Let’s say if your PFC switching frequency is being pushed to 65, 140, 200, 300 kilohertz, you ideally want 10 times the bandwidth of the switching frequency for the current sensor.
Smart manufacturing
When it comes to smart manufacturing and the smart factory, it’s really about automation and data exchange. In a system where powered devices are connected to an intelligent infrastructure and the internet, you’ll also need power conversion. Power monitoring and management are critical to the optimal operation of a smart assembly process, with everything being measured in real-time. There are various locations in an automated system where an AMR current sensor can be deployed to take advantage of its accuracy, bandwidth, and step response. If you have a highly accurate sensor, then you can optimize your process and increase efficiency and productivity.
This performance advantage can be further leveraged by using AMR current sensing to determine how much the processor is being used, especially for applications involving AI, the Cloud, and data storage. AMR current sensors can also enable the use of power tracking for performance monitoring’s sake, optimization of processor loading and thermal management.
Looking forward
Whether it is for advanced EVs, entire smart factories, UPS, inverters or motor drive, efficient and cost-effective power management is key to optimal performance. In applications from driving motors or powering 5G telecom, you want to be operating much faster and more effectively. Advanced current sensing enables a higher level of control, with a higher efficiency, at higher frequencies and temperatures.
The next generation of embedded devices must be able to serve the latest application spaces in the most efficient and cost-effective manner. Using AMR-based current sensing solutions to ensure that the electronics are performing at their best will pay off in cascading benefits throughout the entire system. There is no precision without feedback. Precise fast current feedback enables the highest levels of efficient and safe operation in an advanced powered circuit.
For more information about ACEINNA Current Sensing, please visit https://www.aceinna.com/current-sensors
Author Bio
Khagendra Thapa, VP of Business Development of ACEINNA’s Current Sensing Business, has over 22 years of business management and leadership experience in the electronics equipment and semiconductor industry. Mr. Thapa holds a Bachelors degree in Electronics and Communication, a Master degree in Power Electronics from University of Birmingham in UK and MBA from Manchester Business School in UK. He started his career in graduate management training program in UK. With a strong engineering and business background, he has held various senior roles as a WW Strategic Marketing Manager, Business Unit Director and Senior Director of Business Development in the past both in UK and USA.