The market for lithium-ion batteries is enjoying a high rate of growth – and for good reason: Compared to other energy storage solutions, they offer greater energy density and voltage combined with smaller footprints, more load cycles, and longer lifespans. According to the Avicenne Energy Analysis 2015, less than 10,000 t of Li-ion cathodes were sold in 2000, but by 2014 this figure had increased to over 100,000 t. Market experts forecast a rise of 10% in terms of MWh between 2014 and 2025; other studies predict a similar increase during the same period.
Smartphones, tablets, and portable PCs are the main drivers, with the majority of manufacturers of plug-in hybrid and electric cars now preferring Li-ion batteries. Further target applications include all types of electrically-powered vehicles, e.g. e-bikes, e-scooters, e-boats, fork lift trucks, lawnmowers, and wheelchairs, as well as energy storage systems, photovoltaic backup systems, uninterruptable power supplies (UPS), medical equipment, electric tools, and telecommunication applications.
Cylindrical Li-ion cells
Cylindrical Li-ion cells are beginning to play a central role in the industrial sector. Their design, which includes a solid housing around each individual cell, ensures a high level of safety. Furthermore, they are relatively cost-effective and available in the same form factor for a long period of time, meaning a technology upgrade is fairly fast and easy. Samsung SDI has been the global market leader for cylindrical Li-ion cells since 2010. Its portfolio starts with models that provide a maximum discharge current of between 6A and 8A and whose nominal capacity ranges from 2150mAh to 3450mAh. Vehicles such as e-scooters, golf carts or lawnmowers require cells with a capacity of 1800mAh to 3300mAh and a charge voltage of 4.125V or 4.2V. Cells designed for temporary peak currents of up to 30A are available for applications capable of delivering extremely high temporary discharge currents. Their capacity rating goes from 2000mAh to 2950mAh.
Battery pack design
The cylindrical Li-ion cells are basically only used in battery packs. They form the core of the design. This is because the battery cell determines the parameters and specifications with which the system can operate and which active and passive components are required to ensure top system performance. Rutronik offers its customers extensive help and advice when it comes to selecting the ideal battery and other required components and thus a unique one-stop shopping experience.
The basic design of a battery pack is usually always the same: Several cylindrical cells are connected in parallel (P configuration) and/or in series (S configuration). Next to this is the battery management system (BMS). It has to be carefully coordinated on the basis of an ultra-precise measurement of the charge and discharge currents and the cell voltage. The system typically includes a coulometer, which precisely monitors which electric charge (Q=I × t) flows into and out of the system during a specific period of time. Ideally, each individual cell is monitored within tight tolerances and specification constraints in order to overcharging or unwanted exhaustive discharge.
A cell balancing system ensures that all cells are conditioned equally as far as possible, so that the upstream or downstream charging and discharging processes of the individual cells run as uniformly as possible.
An essential part of the BMS is temperature management of the battery pack and the individual cells. Since adherence to the specified safe working temperature range of a cell has a huge impact on the operational safety, lifespan, and cycle stability of the cell and thus the entire system. The implementation of temperature management is by no means trivial. As temperature sensors can only be fitted to the exterior of the battery cell. However, they can only respond slowly, as temperature increases inside the battery are either detected with a certain delay or insufficiently from the outside. Software models for describing and analyzing the thermal conductivity of the cell are used to counteract this deficiency as much as possible.
At present complex impedances of the single cell are not measured in production applications, such as to determine the state of health as a means of predicting battery life. In the long term, however, this will be a primary function in every future BMS. Impedance spectroscopy, by which the impedance curve of the real and imaginary internal resistance of the cell can be determined, is currently only implemented in the laboratory with stationary measuring points. This requires complex software algorithms to model the impedance curve for comparison of the real analytical and measurement data against the software model of the battery cell. Communication interfaces, usually UART and CAN, but quite often Bluetooth, complete the battery pack. The charge status can be read directly on the battery pack thanks to LED bargraph displays.
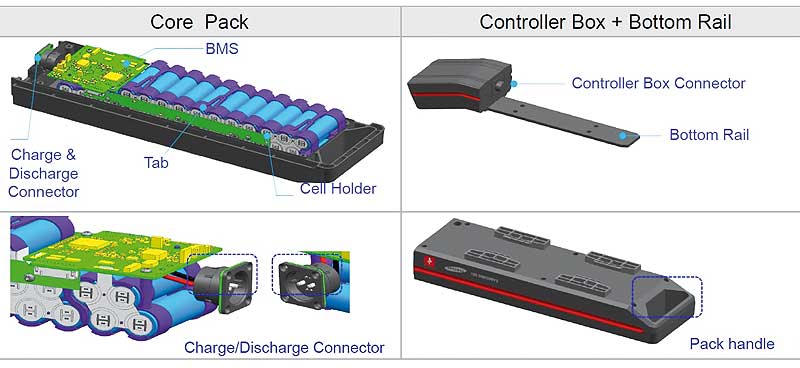
Design of a battery pack with battery management system using an e-bike pack from Samsung SDI as an example; also available at RUTRONIK exclusively for OEMs of e-bikes.
Delicate to handle
Extensive knowledge and careful working practices are decisive not only when designing but also when handling Li-ion batteries. As the cells have been designed for very specific applications. If they are used in a different application or operated in unacceptable conditions, both the battery and the application may be seriously damaged. Strict adherence to specifications is thus imperative for everyone involved in the design or handling process.
Battery manufacturers like Samsung SDI therefore demand the comprehensive documentation of all product processes. This way, customers can be sure of receiving original products, manufactured and shipped to the highest standards, which actually meet all the requirements of the target application. Document management includes dangerous goods documents, manufacturer and product-specific documents as well as release documents for the battery pack manufacturer or battery buyer. This means a vast number of certificates, confirmations, and contracts must be confirmed by both parties. This ensures not only that the products conform to the stringent safety requirements but also that the BMS designer works in strict conformance to the agreed rules.
After selecting a specific battery with the help and support of Rutronik FAEs and product engineers, the customer is issued what is known as a CET document. The customer uses this document to provide detailed information about the application and how the battery is to be used, including the charge time period, maximum peak current pulse, final voltage, etc. The customer must state a competent person and their contact details. This person also has to sign the statement. The company thereby pledges to only use the batteries being purchased for the specified purpose. Without this declaration, no transaction can take place, because the information it contains is provided for the safety of all parties, and is a key element of risk management within the battery business process.
Absolute confidentiality is of paramount importance in this respect. NDAs (Non-Disclosure Agreement) between Samsung SDI and Rutronik as well as between Rutronik and the customer are mandatory.
In addition to the actual quote, the customer also receives the data sheet, which, just like the product use declaration (PUD), must be signed as part of the contractual commitment. The customer is additionally provided with an MSDA (Material Safety Data Sheet), which lists the safety requirements for the specific product in detail, and the recycling documents.
Safe shipment
Seeing as Li-ion batteries are classed as dangerous goods, the distributor is required to comply with further laws and regulations. The ICAO (International Civil Aviation Organization)/IATA (International Air Transport Association) stipulates that batteries being shipped must not be charged more than 30% and that they must only be shipped in limited quantities and separate from other cargo. Correct handling is documented and risks arising from the product indicated in specifically marked shipping documents, Certificates of Conformity (CoC) or dangerous goods information. Furthermore, the safeguarding of end-to-end traceability is essential. In this respect, Rutronik can rely on a tried-and-tested system. A camera-based system simultaneously reads, records, and archives all the label information and recognizes and interprets all types of barcodes. Information about each individual packaging unit can still be retrieved years later thanks to a unique number. The central management of all processes and the processing and archiving of relevant data and documents are the basic prerequisites in the global battery business. Standardization of the process landscape across all continents is particularly important for internationally active customers. At Rutronik, all the processes are fully IT based, thus ensuring their correct execution at all times. All documents and information are saved in a central archive system and linked to the delivery note level. Each and every Rutronik branch office and subsidiary around the globe can access this archive. This way, it is possible to determine which product was where, when, and why. This USP is decisive for safeguarding the future of a company actively involved in the global battery business.
By: Andreas Mangler, Director Strategic Marketing & Communications, Rutronik